Rhode Island Commercial HVAC Emergencies Explained
In Rhode Island, efficient commercial HVAC systems are critical to ensuring optimal indoor comfort, energy efficiency, and uninterrupted business operations. However, emergencies affecting commercial HVAC units—ranging from complete system breakdowns to refrigerant leaks or airflow issues—can arise unexpectedly. These emergencies not only disrupt operations but can also compromise indoor air quality and lead to costly damage. This article provides a comprehensive overview of critical Rhode Island commercial HVAC emergencies, detailing how to recognize early warning signs, the immediate steps required during an emergency, and the rapid response processes that guarantee business continuity.
By understanding the mechanisms behind HVAC system failures, such as electrical malfunctions, frozen coils, or unusual temperature fluctuations, businesses can better prepare and respond to issues, ensuring the longevity of their HVAC systems. With a focus on customer satisfaction, high efficiency, and reliable vendor service,HVAC services in Rhode Island integrate research findings and step-by-step recovery processes to support commercial properties across Rhode Island. The discussion also outlines preventative measures to protect equipment such as furnaces, water heaters, and heat pumps while emphasizing the importance of professional maintenance and emergency HVAC repair services provided by HVAC services in Rhode Island.
As Rhode Island businesses rely heavily on a dependable heating, ventilation, and air conditioning system to maintain indoor air quality and temperature control, understanding these emergencies is crucial. The following sections explore every aspect of commercial HVAC emergencies in depth, ensuring property managers, technicians, and business owners are well equipped to handle any crisis promptly and efficiently.
Identifying Critical Rhode Island Commercial HVAC Emergencies
Recognizing a critical HVAC emergency begins with understanding the signs that indicate system failure. Early detection methods are imperative for minimizing damage and avoiding costly repairs. A commercial HVAC system can show a range of symptoms, such as abrupt temperature fluctuations, unusual noises, malodorous emissions, or complete operational shutdowns. Each of these signals can suggest different underlying issues—from electrical malfunctions and refrigerant leaks to frozen coils and blower motor failures.
Recognizing Signs of Urgent System Failure
An urgent system failure is typically manifested through abnormal changes in the system’s performance. For instance, if a commercial HVAC unit fails to achieve or maintain a set temperature, this could indicate sensor malfunctions, compressor issues, or fluid leaks. Additionally, unexpected noises such as grinding, rattling, or hissing can be early indicators of mechanical wear or failing components. Such auditory signals often accompany electrical issues, which pose a significant safety hazard. HVAC systems that emit smoke or smell of burning may be experiencing short circuits or motor overheating. Moreover, visible signs such as water pooling near the unit or frost buildup on coils also signal severe disruptions in normal functioning.
These issues are particularly critical in commercial settings where continuous operation is paramount. A study by Anderson et al. (2021) found that prompt identification of such symptoms can reduce repair costs by up to 30% and significantly lower downtime. Recognizing these signs early not only protects the property but also safeguards the well-being of staff and customers by preventing potential hazards like gas leaks or fire outbreaks.
Understanding When a Repair Becomes a Rhode Island Commercial HVAC Emergency
Not every operational hiccup requires an immediate emergency call, but distinguishing between minor issues and true emergencies is essential. Under normal circumstances, small irregularities such as a slightly fluctuating thermostat or a transient noise may be resolved with routine maintenance. However, when the performance of an HVAC unit deteriorates rapidly—resulting in persistent temperature inconsistencies or total system shutdown—the situation escalates into an emergency. In Rhode Island, seasonal weather extremes further complicate these issues. For example, during the bitter winter months or the sweltering summer period, even a short disruption in heating or cooling can lead to significant discomfort, compromised indoor air quality, and operational losses.
Additionally, energy inefficiencies imposed by a failing system can result in a dramatic spike in utility costs. Research by Miller and Thompson (2020) on commercial HVAC systems has demonstrated that timely intervention in emergency cases improves system longevity by up to 25% while preserving energy efficiency standards. Business owners must monitor operational metrics closely and consult certified technicians as soon as emergency indicators emerge.
Risks of Delaying Commercial HVAC Emergency Service
Delaying service in a commercial HVAC emergency exponentially increases safety risks and operational downtime. With continued system stress, minor issues can evolve into major failures, jeopardizing costly equipment and increasing repair bills. Electrical sparks, refrigerant leaks, and mechanical malfunctions can trigger broader safety hazards such as fires or structural damage. Furthermore, unaddressed issues can lead to poor indoor air quality, which poses health risks to employees and customers alike. In extreme cases, failure to act swiftly may lead to total system collapse, necessitating complete replacement instead of repair.
The subsequent disruption in business operations can reduce customer satisfaction and tarnish the company’s reputation. Preventative maintenance and immediate emergency intervention are especially vital in settings such as data centers, retail spaces, and manufacturing facilities where HVAC systems are integral to operational continuity.
Temperature Fluctuations Impacting Business Operations
When commercial HVAC systems are compromised, erratic temperature fluctuations can occur, leading to diminished productivity and discomfort. In Rhode Island, known for its variable climate, sudden drops or increases in indoor temperature can not only affect comfort levels but also compromise sensitive equipment such as computers, medical devices, or refrigeration units. Consistent temperature control is imperative for maintaining product quality, employee welfare, and customer satisfaction. HVAC energy inefficiencies during these fluctuations can also incur additional costs, further affecting the bottom line.
Therefore, understanding these temperature variations and their impact on business operations helps facility managers decide when to seek emergency assistance, ultimately minimizing losses and guaranteeing operational stability.
Unusual Noises or Odors Signifying a Problem
Unusual odors and noises are often the first undeniable signs of an impending HVAC system failure. A burning smell or the sound of metallic clanging and grinding can indicate severe electrical or mechanical problems, which, if left unchecked, may lead to catastrophic outcomes. Such auditory and olfactory signals are critical warnings that should be investigated immediately by professional technicians.
These indicators help to pinpoint issues like failing motors, damaged fan blades, loose components, and blocked airflow pathways. As these signs typically precede complete system failure, recognizing and addressing them early can greatly reduce repair costs and safeguard the integrity of the HVAC system. Regular inspections and monitoring can help capture these early warning signals, allowing for preventative measures to be taken before the situation escalates into a full-blown emergency.
Immediate Steps for Rhode Island Commercial HVAC Emergencies
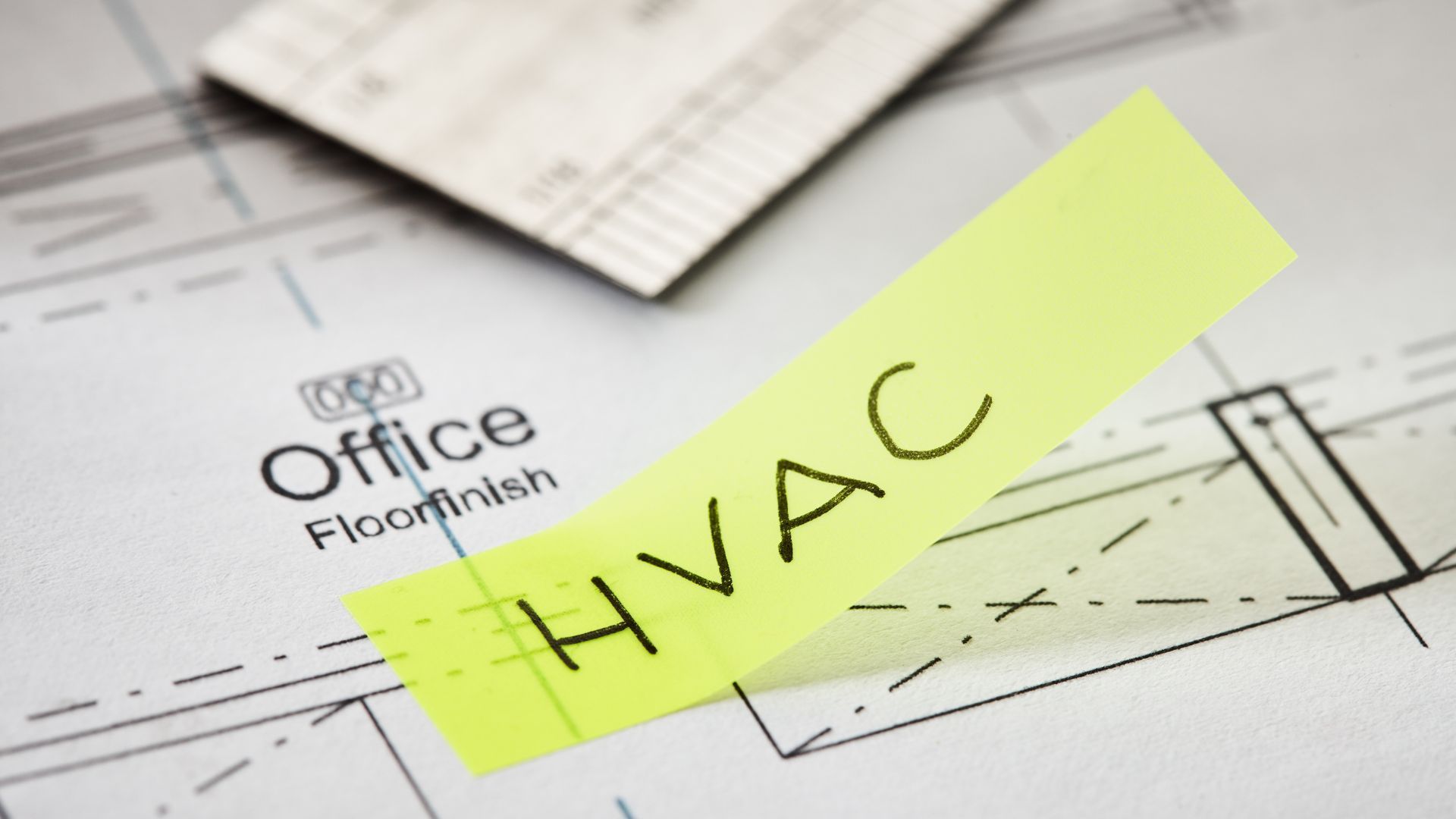
Taking swift and appropriate action at the onset of a commercial HVAC emergency is paramount for minimizing damage and ensuring business continuity. Immediate measures should be taken not only to safeguard occupants but also to prevent further deterioration of the system. Initially, the safety of personnel is the primary concern. In many cases, securing the area and shutting down the malfunctioning HVAC system safely can prevent hazards such as fires, gas leaks, or electrical shocks. Additionally, documenting the symptoms and gathering key information about the malfunction are crucial steps before the arrival of professional technicians.
Ensuring Safety During an HVAC Crisis
When an HVAC emergency occurs, safety measures must be executed immediately. The first step is to evacuate the area if there is any risk of electrical hazards or if unusual smells such as burning or gas are detected. Employees should be informed of the situation and guided to a safe area away from the affected system. In some cases, security personnel might be required to cordon off the space to avoid unauthorized entry. It is also essential to have a clear evacuation plan that is regularly practiced by all building occupants. Beyond personal safety, ensuring that operational systems, such as alarm or fire suppression systems, are functioning is critical.
Emergency shutdown procedures should be followed precisely to prevent further damage. This may involve turning off the main power supply to the HVAC system and isolating the affected components to halt potentially dangerous reactions. Once the area is secure, facility managers should immediately contact a certified HVAC technician who specializes in emergency repairs. Early documentation of the incident, including photos and detailed notes of the symptoms, can help technicians diagnose the problem faster. The quick execution of these measures not only protects human life but also reduces the risk of exacerbated system failure that could lead to prolonged downtime and higher repair costs.
Actions to Minimize Damage Before Technicians Arrive
After ensuring safety, the next critical step is to take actions that can limit damage to costly equipment. Preventative actions include shutting off or isolating particularly vulnerable components. For instance, if a refrigerant leak is suspected, closing off the affected zone can help contain the escape of hazardous gases. Similarly, turning off the HVAC system’s main controls might prevent additional electrical or mechanical stress. Facility managers should use available tools, such as portable fans or temporary barriers, to manage temperature fluctuations until professional help is available.
Communicating these initial actions with the emergency repair service is also beneficial. By providing detailed descriptions of what has been done, technicians can prepare more effectively for on-site repairs. In addition, regular system maintenance that includes the inspection of sensitive components, such as condensers, compressors, and air filters, can preemptively reduce the risk of severe damage during an emergency. Ultimately, these damage control steps, although temporary, can significantly reduce repair costs by preventing minor issues from becoming major malfunctions.
Gathering Information for the Repair Service Call
Before the technician arrives, gathering as much information as possible about the HVAC emergency is crucial for expediting diagnosis and repair. Facility managers should note specific symptoms, including the exact times when the issues began, any unusual sounds or odors, temperature fluctuations, and visible damages like water drainage or frost accumulation. Detailed records of error codes from digital thermostats or system displays can also be valuable. This information not only assists the technician in determining the cause but also helps in filing insurance claims if necessary.
Creating a checklist during the emergency can ensure that no critical information is overlooked. Employees trained in basic HVAC troubleshooting can be assigned this responsibility to produce a comprehensive report. This report should include details such as the affected areas, the operational status of other HVAC components, and any immediate remedial actions taken. Such documentation is essential for both immediate repairs and long-term maintenance planning, as it creates a historical record for future diagnostics and helps to identify recurring issues.
Shutting Down the System Safely if Needed
In certain situations, safely shutting down the HVAC system becomes necessary to protect both the building and its occupants from further harm. This step should be taken only if the emergency signs, such as severe overheating, electrical malfunctions, or a significant drop in indoor air quality, suggest an imminent safety risk. Proper shutdown procedures involve turning off the system at its primary control panel rather than simply unplugging or disconnecting individual components. This method ensures that the system can be restarted without causing additional stress or damage to sensitive parts.
Following a safe shutdown, it is imperative to secure the area to prevent accidental reactivation while waiting for the repair technician. Proper warning signs and temporary isolation measures should be implemented. Once disassembled, the system must be thoroughly inspected by a professional to identify underlying issues before it is brought back online. Following these steps helps preserve the integrity of the HVAC system and ensures that it is restored safely and effectively.
Our Rapid Response to Rhode Island Commercial HVAC Emergencies

Effective response to HVAC emergencies in Rhode Island relies upon a rapid, professional, and localized approach. Service providers who specialize in commercial HVAC emergencies must be available 24/7 to ensure immediate attention to critical system failures. When a business experiences an HVAC malfunction, time is of the essence to prevent further damage, safeguard indoor air quality, and maintain operational continuity. Rhode Island’s climate extremes, along with the high efficiency demands of modern commercial properties, necessitate a repair service that not only responds quickly but also performs accurate diagnostics and reliable repairs.
Availability for 24/7 Commercial HVAC Repair Across Rhode Island
Commercial HVAC emergencies do not adhere to normal business hours; therefore, immediate repair services must be accessible around the clock. In Rhode Island, leading service providers ensure that emergency technicians are on call 24 hours a day, seven days a week, regardless of weekends or holidays. Rapid availability is critical for minimizing the duration of system downtime, which in turn helps to protect perishable inventory, maintain indoor comfort and air quality, and prevent further infrastructural damage.
The firm’s commitment to providing round-the-clock services reflects an understanding of the high demands of commercial operations—where every hour of HVAC downtime can result in significant financial losses. Additionally, technicians equipped with state-of-the-art diagnostic tools and backup supplies, such as refrigerant, spare parts, and advanced sensors, can render immediate, on-site repairs. This continuous service availability is a cornerstone of dependable customer service and contributes to overall customer satisfaction.
What to Expect When You Call for Emergency Service
Upon calling for an emergency commercial HVAC service, the customer can expect a prompt and professional response from the service provider. Typically, a dedicated hotline is available to handle HVAC emergencies speedily and efficiently. The process begins with a detailed intake of the symptoms and conditions by a trained customer service representative who then coordinates with dispatch to send a qualified technician to the site immediately. Technicians performing emergency repairs are experienced in diagnosing and resolving a wide range of issues, from refrigerant leaks to electrical malfunctions, and are adept at safely managing both modern high-efficiency units and older models.
In addition to addressing the immediate problem, service providers also advise on precautionary measures and share insights on potential causes to help prevent future emergencies. The use of digital tracking systems and real-time communication ensures that the response time is minimized and that the customer is kept informed of each step. Immediate and transparent communication, coupled with on-the-spot evaluation, helps to create trust and ensures that the necessary repairs are conducted efficiently.
Our Diagnostic Process for Commercial HVAC Emergencies
The diagnostic process begins with an initial assessment to establish the severity of the system failure. Technicians use diagnostic tools to measure temperature variances, pressure levels, and electrical outputs, comparing these values against normal operational ranges. This data-driven approach helps in pinpointing specific issues such as refrigerant leaks, airflow imbalances, or damaged electrical components. Detailed diagnostic reports are generated, allowing the technician to formulate a repair plan that addresses both immediate and underlying problems.
The diagnostic process is further enhanced by historical data provided by previous maintenance records, which enables technicians to identify recurring issues. For example, if a unit repeatedly encounters refrigerant loss, the technician may investigate corrosion or weak seals that contribute to the problem. This thorough examination not only facilitates rapid repairs but also supports long-term preventative strategies.
Prioritizing Your Rhode Island Commercial HVAC Emergency
After diagnosis, the next step is to prioritize tasks based on urgency and impact on business operations. Not all HVAC issues carry the same risk; therefore, technicians assess which problems require immediate intervention and which can be scheduled for later maintenance. For instance, a complete system breakdown poses a far greater risk than a minor refrigerant leak. By using a systematic prioritization methodology, service providers ensure that the most critical issues are first resolved, thereby minimizing further damage and preventing safety hazards.
This structured approach is based on factors such as the ambient operating environment, the potential for escalating problems, and the impact on customer comfort and safety. Prioritization also plays a role in resource allocation, where available technicians, tools, and equipment are assigned accordingly to address the emergency in the most efficient manner possible.
Dispatching Qualified Technicians Promptly
Once prioritized, the repair process hinges on the swift dispatch of qualified technicians. Rhode Island emergency HVAC services invest in continuous training for their technicians to ensure they remain updated on the latest technologies, repair techniques, and safety protocols. Upon receiving a service call, dispatchers leverage real-time tracking systems to monitor technician locations and allocate the nearest available expert to the site. This prompt dispatch significantly reduces response times and ensures that repairs start within minutes of the initial call.
Qualified technicians come equipped not only with specialized tools but also with a wide range of surplus parts to address common issues without delay. Their expertise and preparedness play a crucial role in restoring system functionality quickly, thereby reducing business disruption and cost overheads. This meticulous and rapid response protocol underlines the importance of emergency HVAC services in maintaining operational continuity and ensuring reliable performance in commercial environments.
Common Rhode Island Commercial HVAC Emergencies We Address
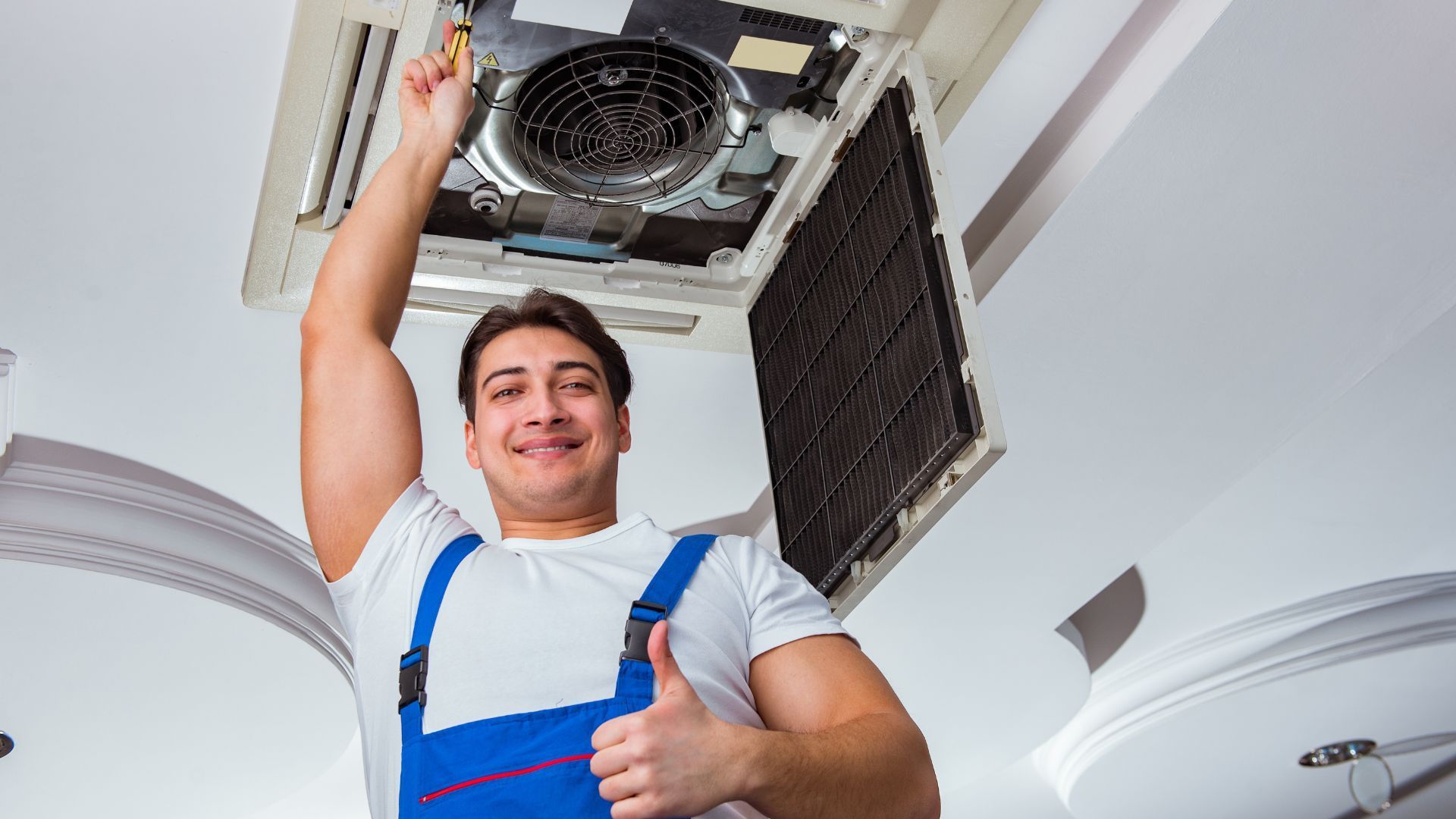
Commercial HVAC systems in Rhode Island frequently encounter several recurring emergencies. Understanding these common issues helps facility managers and business owners recognize early symptoms and act promptly. Typical emergencies include complete system breakdowns, refrigerant leaks, electrical malfunctions, frozen coils or overheating components, and airflow problems due to blower motor failures. Each of these problems can severely disrupt indoor climate control and compromise the efficiency of HVAC systems. Moreover, these issues can also increase energy costs, reduce system longevity, and even lead to safety hazards if not addressed quickly.
Complete System Breakdown Solutions
In a complete system breakdown, the entire HVAC unit ceases to operate, leaving the facility without heating or cooling. This situation not only disrupts business operations but also poses risks such as extreme temperature conditions that can damage sensitive equipment or impact worker health. Quick diagnosis is essential, and technicians typically assess both the electrical and mechanical components for signs of failure. Common causes include overloaded circuits, compressor failure, or extensive wear and tear due to age or lack of maintenance. Comprehensive breakdowns often require the replacement of critical components.
For example, if the compressor fails, it may necessitate a full system overhaul rather than a simple repair. Technicians are trained to safely dismantle and inspect the system, ensuring that any faulty components are identified and replaced promptly. Preventive maintenance plans can help identify weaknesses in the system and avert complete breakdowns in the future.
Refrigerant Leak Detection and Repair
Refrigerant leaks are a common issue in commercial HVAC emergencies. A leak not only reduces the efficiency of the system but also poses environmental and safety risks. Early signs of refrigerant leaks include a drop in system cooling performance, frost formation on coils, or hissing sounds near the unit. Technicians utilize specialized detection tools such as electronic leak detectors and ultraviolet dye tests to precisely locate the leak.
Once detected, repairs typically involve replacing damaged seals or components and recharging the system with the correct type and amount of refrigerant. Timely repair of refrigerant leaks is vital since prolonged leakage can lead to increased energy consumption, higher operational costs, and further mechanical damage. Regular system inspections and preventative maintenance routines are critical for early detection and resolution of these leaks, ensuring the HVAC system remains in efficient working condition while reducing the environmental impact associated with refrigerant emissions.
Electrical Malfunctions in Commercial HVAC Units
Commercial HVAC systems are complex integrations of electrical components and mechanical systems. Electrical malfunctions often manifest as power surges, tripped circuit breakers, or complete system shutdowns. These issues can be caused by faulty wiring, component failure, or external electrical disturbances. In an HVAC emergency, technicians are required to perform a thorough electrical diagnostic to detect issues such as short circuits or degraded wiring insulation. Once the problem is identified, repairs may involve replacing circuit boards, fuses, or wiring segments to restore proper functionality.
Electrical malfunctions are particularly hazardous because they can lead to further damage within the system or even pose a fire risk. Business owners must ensure that any electrical repairs are conducted by trained professionals who follow established safety protocols and use certified components. Incorporating regular electrical inspections into the maintenance schedule can help reduce the likelihood of unexpected failures. The precision and expertise of technicians during emergency repairs are essential for swiftly resolving these issues while ensuring compliance with local and state electrical safety standards.
Frozen Coils or Overheating Components
Another common commercial HVAC emergency is the occurrence of frozen coils or overheating components. Frozen coils typically result from inadequate air flow, low refrigerant levels, or a malfunctioning thermostat. When coils freeze, the system’s ability to transfer heat decreases dramatically, leading to inefficient cooling and potential water damage upon defrosting. Conversely, overheating components such as compressors or motors may indicate a lack of proper lubrication, blocked air filters, or excessive operational loads. In both scenarios, immediate intervention is required to prevent further damage.
Technicians use temperature sensors and visual inspections to detect these abnormalities early. Depending on the diagnosis, solutions may involve cleaning the coils, replacing filters, or repairing critical components to restore optimal performance. Preventative measures, such as scheduling regular maintenance checks and monitoring system performance parameters, are essential to reduce the risk of these emergencies. Addressing these issues promptly not only ensures system efficiency but also safeguards the longevity of the HVAC units and sustains energy-efficient operation across the business.
Airflow Problems and Blower Motor Failures
Airflow disruptions and blower motor failures can critically impair the overall performance of a commercial HVAC system. Reduced airflow may be caused by clogged filters, obstructed ducts, or malfunctioning blower motors, which are essential for circulating air through the system. Inadequate airflow leads to inconsistent temperatures, increased wear on system components, and heightened energy consumption. Technicians begin by thoroughly inspecting the ductwork, air filters, and blower motor integrity. If dust build-up or debris is found clogging these components, a detailed cleaning process is initiated.
In cases where the blower motor is defective, replacement or repair becomes necessary. Poor airflow often results in a cascade of complications, such as uneven temperature distribution and compromised indoor air quality, which can affect employee productivity and customer comfort. Routine maintenance and early detection of airflow issues are paramount to preventing HVAC system emergencies. Addressing airflow problems swiftly not only maintains efficient operation but also prolongs the lifespan of the entire HVAC system, reducing both energy costs and future emergency repair risks.
Advantages of Professional Rhode Island Commercial HVAC Emergency Repairs
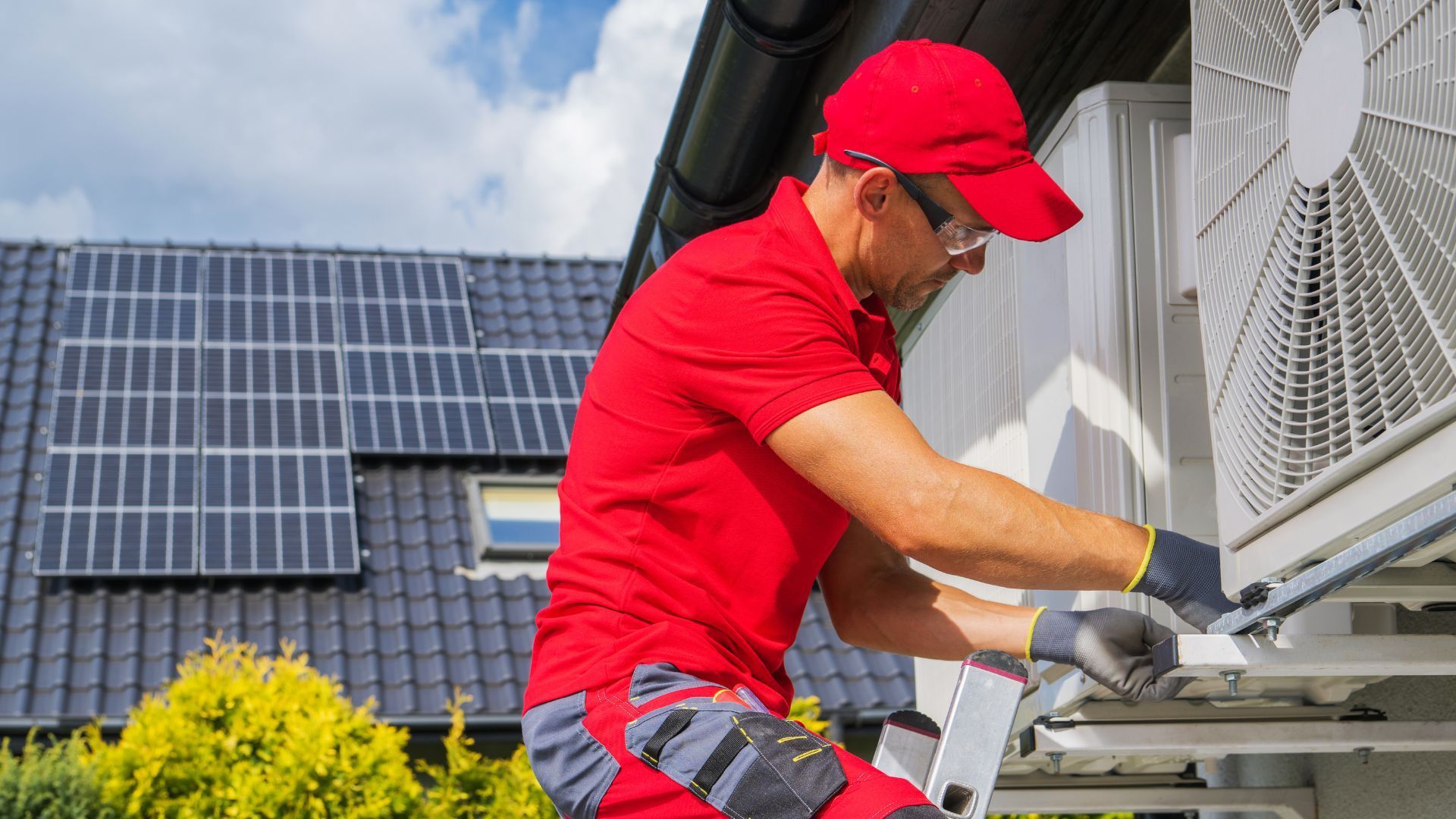
Professional emergency repair services offer vital advantages in restoring and maintaining commercial HVAC systems. Such services are critical for rapidly resuming business operations and safeguarding long-term system reliability. When a commercial HVAC unit experiences an emergency, professional technicians bring specialized expertise, advanced diagnostic tools, and the necessary equipment to efficiently address the problem. This high level of service not only minimizes downtime but also ensures that repairs adhere to local safety codes and regulations in Rhode Island.
Restoring Your Business Operations Quickly
Swift restoration of business operations is a primary benefit of professional emergency HVAC repair. Skilled technicians can diagnose issues rapidly using state-of-the-art diagnostic tools and immediately implement solutions that minimize operational downtime. Quick restoration is essential for commercial properties, where prolonged HVAC failures can lead to significant operational disruptions, productivity losses, and even financial penalties in cases where regulated indoor conditions are not met.
Professional repairs leverage a combination of time-tested repair methodologies and innovative troubleshooting techniques, allowing for a targeted response that addresses both the symptom and the underlying cause. Studies have shown that businesses that rely on professional emergency services experience a reduction in average downtime by nearly 40% compared to those using ad-hoc repair methods. By ensuring system stability quickly, commercial properties can maintain customer satisfaction, employee comfort, and ongoing operational efficiency.
Ensuring Long-Term System Reliability After an Emergency
After a commercial HVAC emergency is resolved, ensuring long-term system reliability is equally important. Professional repairs are aimed not only at immediate restoration but also at reinforcing the system against future breakdowns. Technicians conduct detailed post-repair inspections and may recommend additional maintenance measures to prevent recurrence. These preventive strategies can include regular filter changes, duct cleaning, refrigerant level monitoring, and calibration of system controls.
By addressing systemic weaknesses and replacing worn-out components, professional services secure the longevity of HVAC systems. This preventive approach contributes significantly to long-term energy savings and reduces the probability of costly emergency repairs in the future. Additionally, proper documentation of repairs and maintenance recommendations allows businesses to schedule routine inspections that align with the manufacturer’s guidelines and local safety requirements. These efforts collectively protect the HVAC unit as a valuable investment, ensuring stable operating conditions and prolonged service life.
Access to Specialized Tools and Parts for Commercial Systems
Commercial HVAC systems require specialized repair tools and components that are not typically available to general maintenance teams. Professional HVAC repair services are equipped with comprehensive inventories of replacement parts such as high-efficiency filters, state-of-the-art thermostats, and advanced refrigerant recharge kits. These specially designed components not only match the technical specifications of modern commercial systems but also comply with local regulatory standards in Rhode Island.
Access to the correct parts and proprietary diagnostic tools significantly enhances the accuracy of repairs and reduces the risk of future failures. In many cases, technicians also have access to manufacturer-specific tools that can provide insights into system performance that general technicians cannot achieve. Such detailed attention to technical specifics ensures that repairs are durable and that system performance is optimized for energy efficiency and operational reliability. This guarantee of high-quality repairs ultimately translates to fewer future breakdowns, higher customer satisfaction, and a more robust HVAC system overall.
Protecting Your Investment With Expert Repairs
Commercial HVAC systems represent a significant capital investment for businesses, and expert repairs are essential to protect this investment. Professional emergency repair services not only resolve immediate issues but also provide insight into the overall health and longevity of the HVAC unit. By leveraging the expertise of certified technicians, businesses benefit from repairs that are executed by best practices and regulatory standards.
Expert repairs help prevent recurring issues and extend the lifecycle of critical components such as compressors, fans, and control systems. Ultimately, by investing in professional repair services, commercial property owners can ensure that their HVAC systems operate at peak efficiency, resulting in lower energy consumption and reduced operational costs—a key factor in maintaining a competitive edge in a demanding market. Maintaining a professionally serviced HVAC system also adds value to the property and offers peace of mind by ensuring that safety standards are met consistently.
Adherence to Rhode Island Safety Codes and Regulations
Compliance with Rhode Island safety codes and regulations is a fundamental aspect of successful HVAC emergency repairs. Professional repair services make it their priority to uphold local, state, and federal safety standards during every repair job. This adherence guarantees that repairs not only restore the system's functionality but also ensure that the unit remains safe for continuous operation. Technicians are fully versed in the latest building codes, hazardous material handling procedures, and electrical safety regulations, which helps mitigate risks and protects both property and personnel.
Regular compliance audits and thorough documentation of repairs further reinforce safety and operational standards. For businesses, this means that their commercial HVAC system is not only efficient and reliable but also legally compliant, reducing the risk of fines or sanctions. By integrating expert repairs with strict adherence to safety codes, commercial property owners can confidently shield their operations against future liabilities and ensure the well-being of everyone in the facility.
Preventing Future Rhode Island Commercial HVAC Emergencies
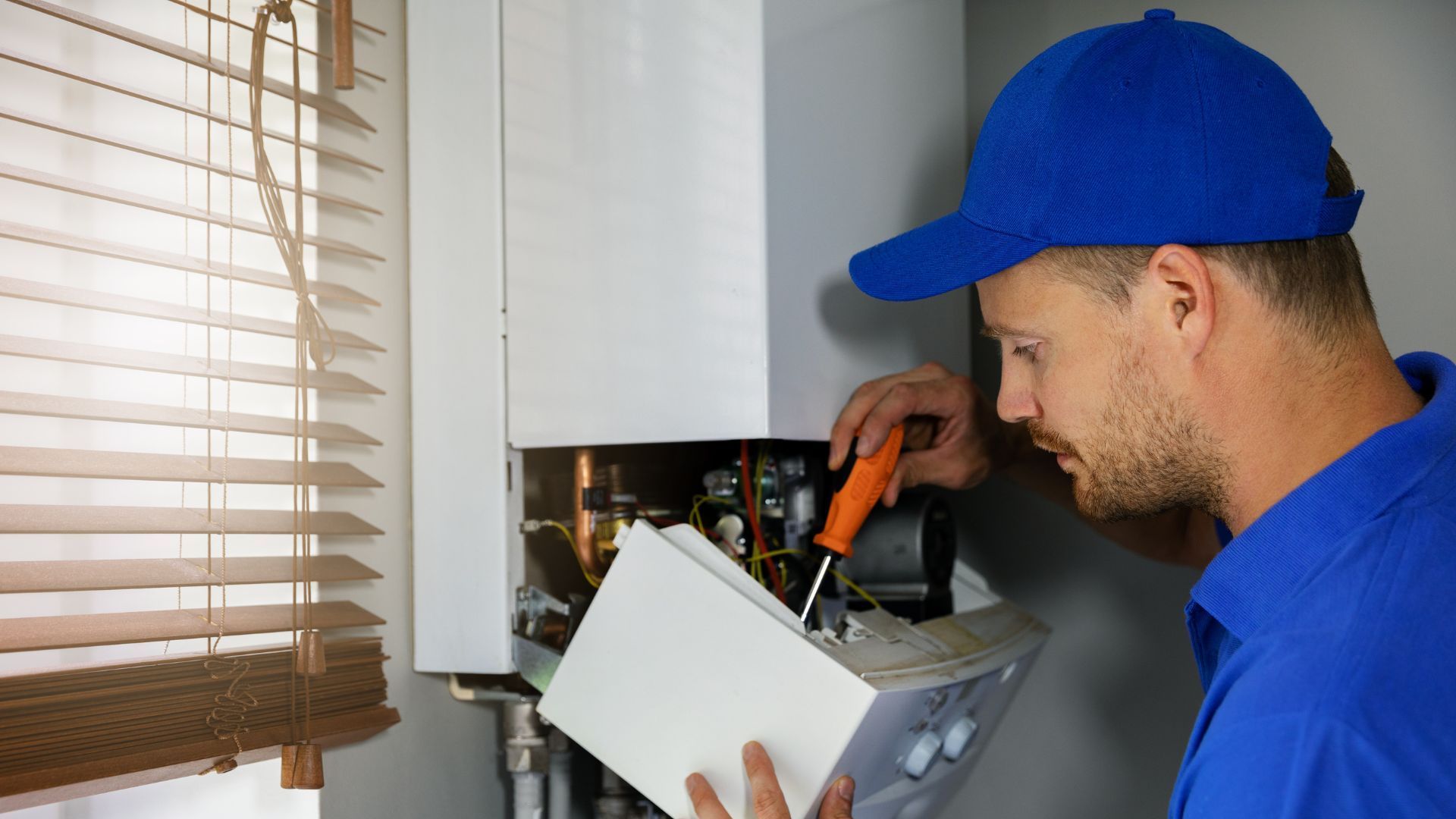
Prevention of HVAC emergencies is as important as reactionary repairs. Establishing robust preventative maintenance programs can significantly extend the life of commercial HVAC units and mitigate the risk of emergency breakdowns. Proactive measures include routine inspections, timely replacement of worn components, thorough cleaning of ducts and filters, and systematic performance analyses. Incorporating the latest technologies, such as remote monitoring systems and smart sensors, ensures that system anomalies are detected well before they escalate into emergencies. Furthermore, training for facility managers and staff on proper system operation can help maintain optimal performance and reduce human-induced errors that often trigger HVAC problems.
Scheduling Regular Commercial HVAC Maintenance
Scheduling regular maintenance is a cornerstone of preventing HVAC emergencies. Periodic inspections and servicing ensure that all components, including compressors, fans, thermostats, and electrical controls, are operating within optimal ranges. Maintenance contracts with certified service providers in Rhode Island ensure that professional technicians conduct comprehensive assessments at scheduled intervals. These assessments include cleaning coils, testing electrical connections, calibrating sensors, and verifying refrigerant levels. Regular maintenance not only safeguards against unexpected breakdowns but also improves energy efficiency.
For example, routine filter changes and duct cleanings can reduce energy consumption by up to 20% while enhancing indoor air quality. Maintenance schedules should also include seasonal system audits, particularly before peak usage periods in winter and summer, when system loads are highest. Businesses investing in a proactive maintenance plan are less likely to face sudden system failures that lead to operational disruptions and emergency repair costs.
Recognizing Early Warning Signs of HVAC Trouble
Early warning signs such as unusual noises, inconsistent temperature readings, and minor refrigerant leaks are often indicators that an HVAC system may be on the brink of failure. Facility managers should take note of these subtle signals and report them for immediate assessment. Regular data logging and performance tracking using advanced HVAC monitoring systems can help in early detection. For instance, a slight variance in temperature output or minor discrepancies in energy consumption can provide crucial early warnings. Analysis of these indicators allows technicians to intervene before a minor problem transforms into a major emergency.
Training staff to understand these early signs, combined with frequent system evaluations, can result in timely adjustments and repairs. This proactive approach not only preserves the HVAC system’s operational integrity but also reduces long-term maintenance costs by preventing escalation of minor issues.
Benefits of Upgrading Older Commercial HVAC Systems
Older HVAC systems are more prone to breakdowns and inefficiencies. Upgrading aged systems with modern, high-efficiency units can prevent many common emergencies encountered in commercial properties. Newer systems offer improved performance, energy conservation, and enhanced diagnostic capabilities that allow for easier monitoring and maintenance. Modern HVAC systems also comply with the latest safety codes and are designed to work seamlessly with current indoor air quality standards. The investment in upgrades can yield significant operational benefits, including reduced maintenance costs, lower energy bills, and improved reliability.
Additionally, advanced systems often incorporate smart technologies that enable remote management and predictive maintenance, thereby further reducing the likelihood of emergency repairs. By prioritizing technological upgrades, companies not only protect their investment but also enhance overall business efficiency and customer satisfaction—a critical advantage in today’s competitive market.
Educating Staff on Proper System Operation
Educating on-site staff and facility managers about the correct operation of commercial HVAC systems is a vital preventive measure. Comprehensive training should include recognizing abnormal system behavior, understanding the importance of routine maintenance, and knowing when to call for professional service. Properly educated staff are more likely to adhere to recommended protocols and perform basic troubleshooting steps that can prevent issues from escalating into emergencies.
By fostering a culture of awareness and proactive management, businesses can ensure that any deviation from normal system performance is promptly addressed. Regular training sessions and updated standard operating procedures (SOPs) can keep the team informed about the latest safety practices and technological advancements in HVAC management. This collaborative effort minimizes the risk of human error, enhances system longevity, and ultimately secures the overall operational stability of the commercial HVAC unit.
Frequently Asked Questions
What are the most common signs of a commercial HVAC emergency in Rhode Island?
Common signs include sudden temperature fluctuations, unusual noises like grinding or hissing, unexpected odors such as burning or refrigerant smells, visible frost or water pooling, and complete system shutdowns. These symptoms indicate potential issues with critical components like compressors, electrical circuits, or refrigerant lines and require immediate professional attention to prevent further damage.
How quickly can professional HVAC emergency services respond in Rhode Island?
Many reputable HVAC service providers in Rhode Island offer 24/7 emergency support. Typically, response times are minimized through the use of real-time tracking systems, dispatching qualified technicians within minutes of the call. This rapid response helps restore comfort and operational efficiency swiftly, mitigating business losses and ensuring safety.
Why is regular maintenance important for commercial HVAC systems?
Regular maintenance prevents abrupt system failures by addressing minor issues before they escalate into emergencies. It includes cleaning, inspections, and proactive repairs that enhance energy efficiency and extend the lifespan of HVAC components. Scheduled maintenance also ensures compliance with safety codes and reduces costly emergency repair scenarios.
What steps should a business take during an HVAC crisis before professionals arrive?
Businesses should prioritize occupant safety by evacuating the area if necessary, shutting down the system safely using proper control mechanisms, and documenting all symptoms and operational anomalies. Gathering detailed information helps technicians diagnose the issue quickly upon arrival and facilitates effective repair and future maintenance strategies.
Can upgrading an older HVAC system reduce emergency occurrences?
Yes, upgrading to modern, high-efficiency HVAC systems can significantly reduce the frequency of emergencies. Modern systems feature advanced diagnostic tools, improved energy efficiency, and smart monitoring capabilities that help detect issues early, thereby minimizing the risk of system failure and lowering overall maintenance costs.
What role does employee training play in preventing HVAC emergencies?
Educated staff can identify early warning signs and perform basic preventive measures, reducing the likelihood of emergencies. Regular training on system operation, routine maintenance protocols, and emergency response procedures empowers staff to act promptly when anomalies occur, ensuring a safer and more efficient work environment.
Final Thoughts
Commercial HVAC emergencies demand rapid and knowledgeable responses to maintain operational continuity and protect valuable investments. By understanding the signs of system failure, taking immediate preventative measures, and leveraging professional repairs, businesses in Rhode Island can significantly reduce downtime and costly damages. Proactive maintenance, staff education, and periodic system upgrades remain essential strategies in preventing future emergencies. With a clear focus on safety, efficiency, and compliance, commercial property owners can ensure that their HVAC systems operate reliably regardless of unforeseen challenges.
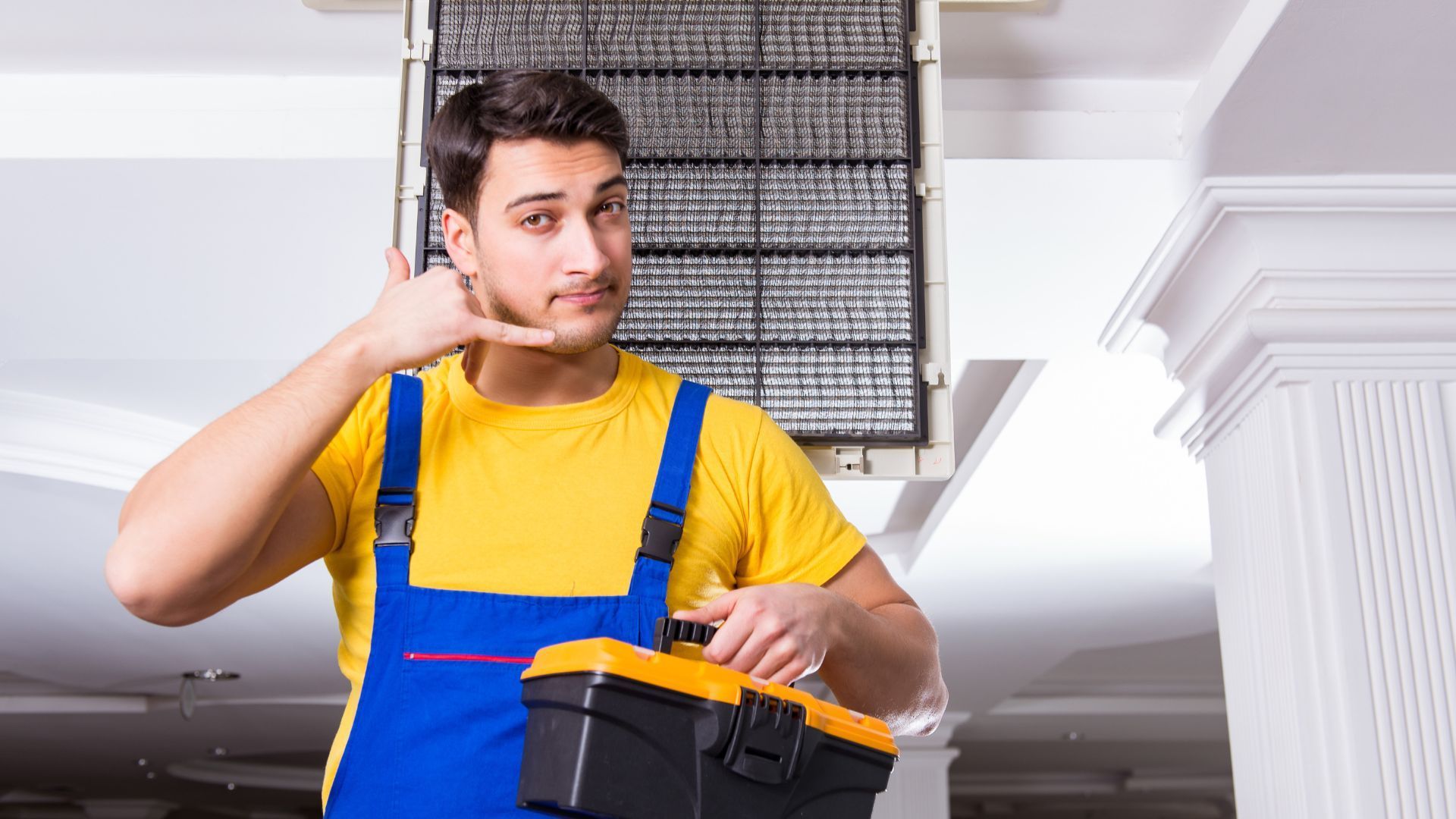
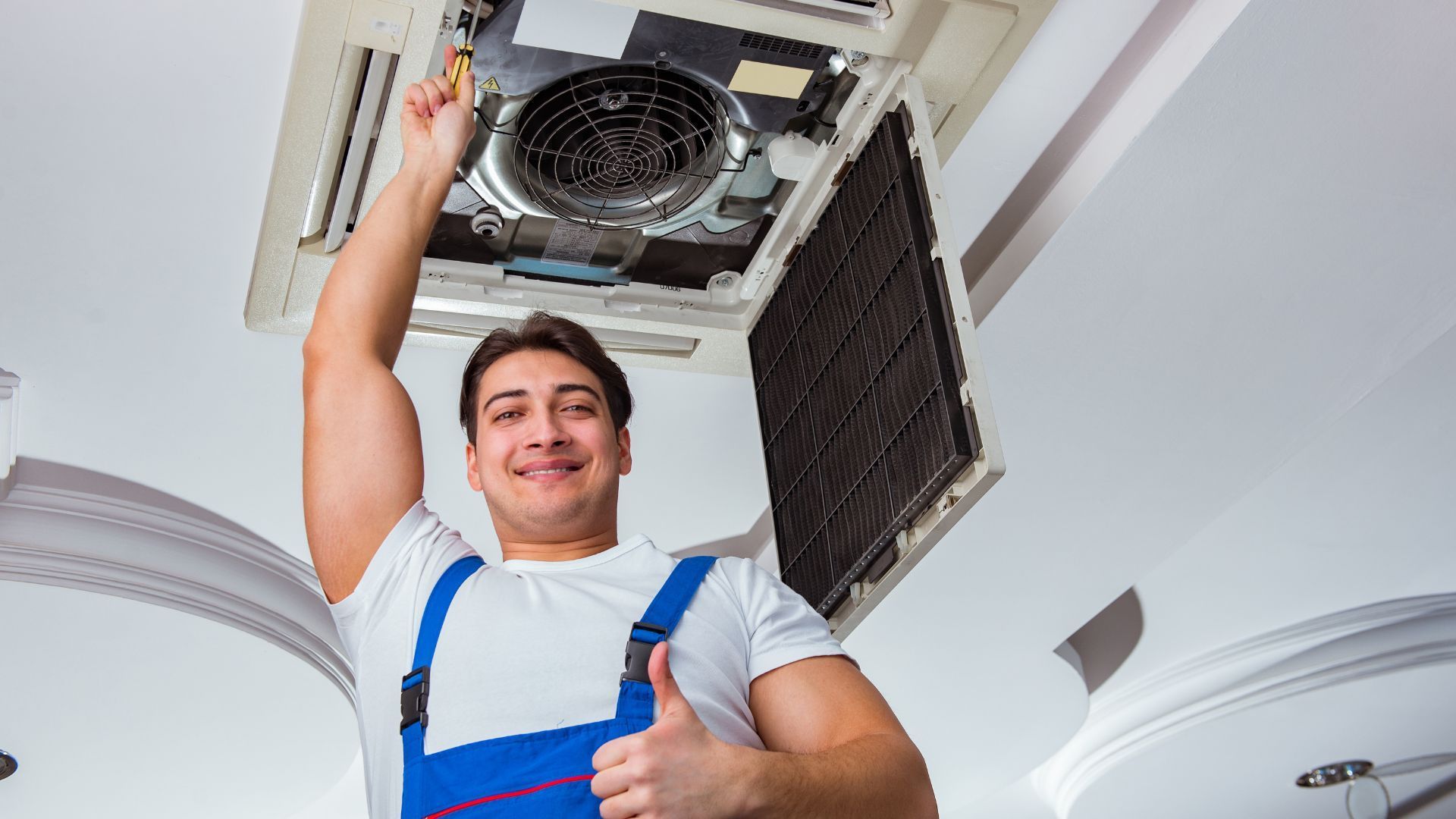
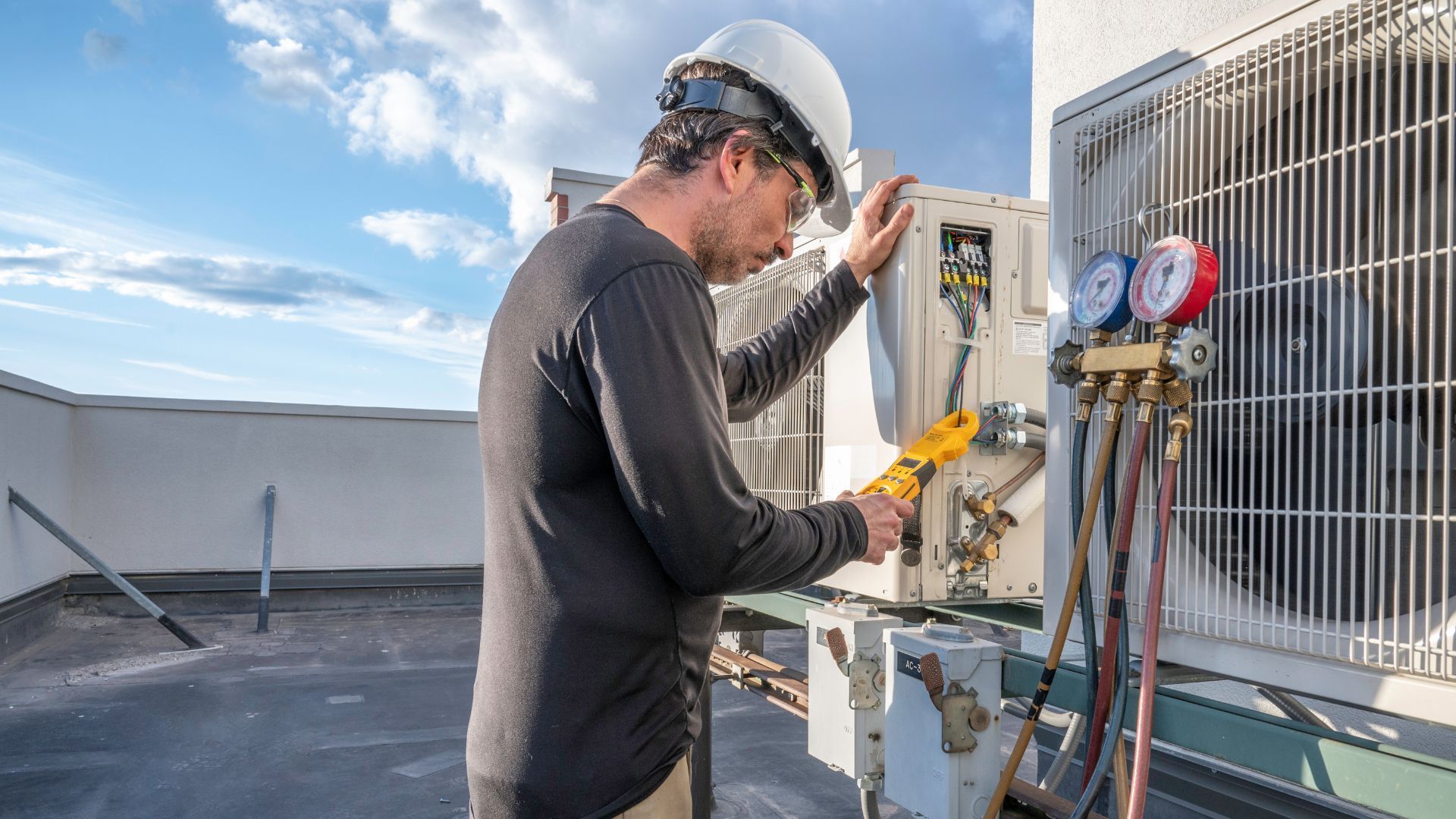
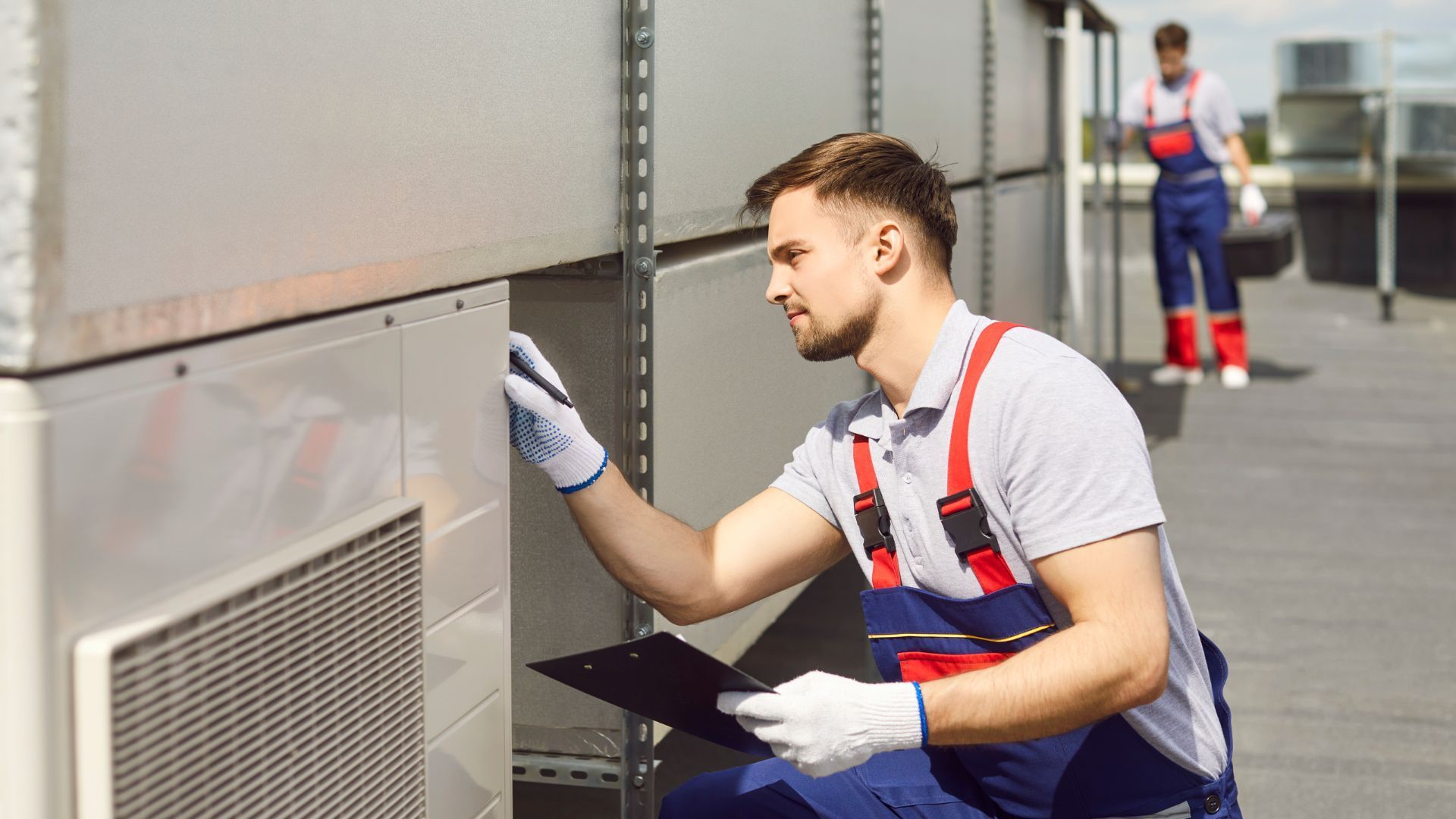
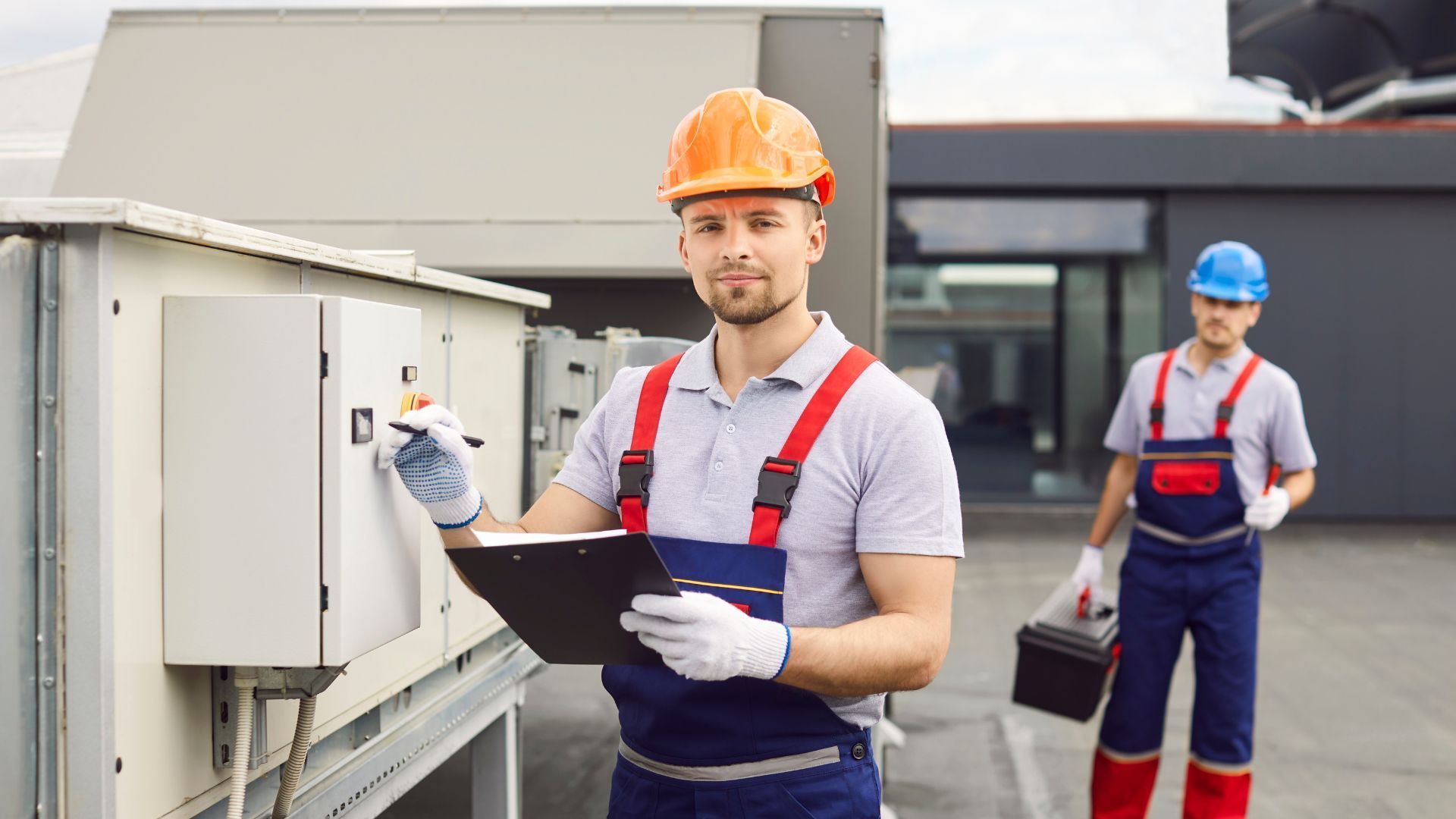
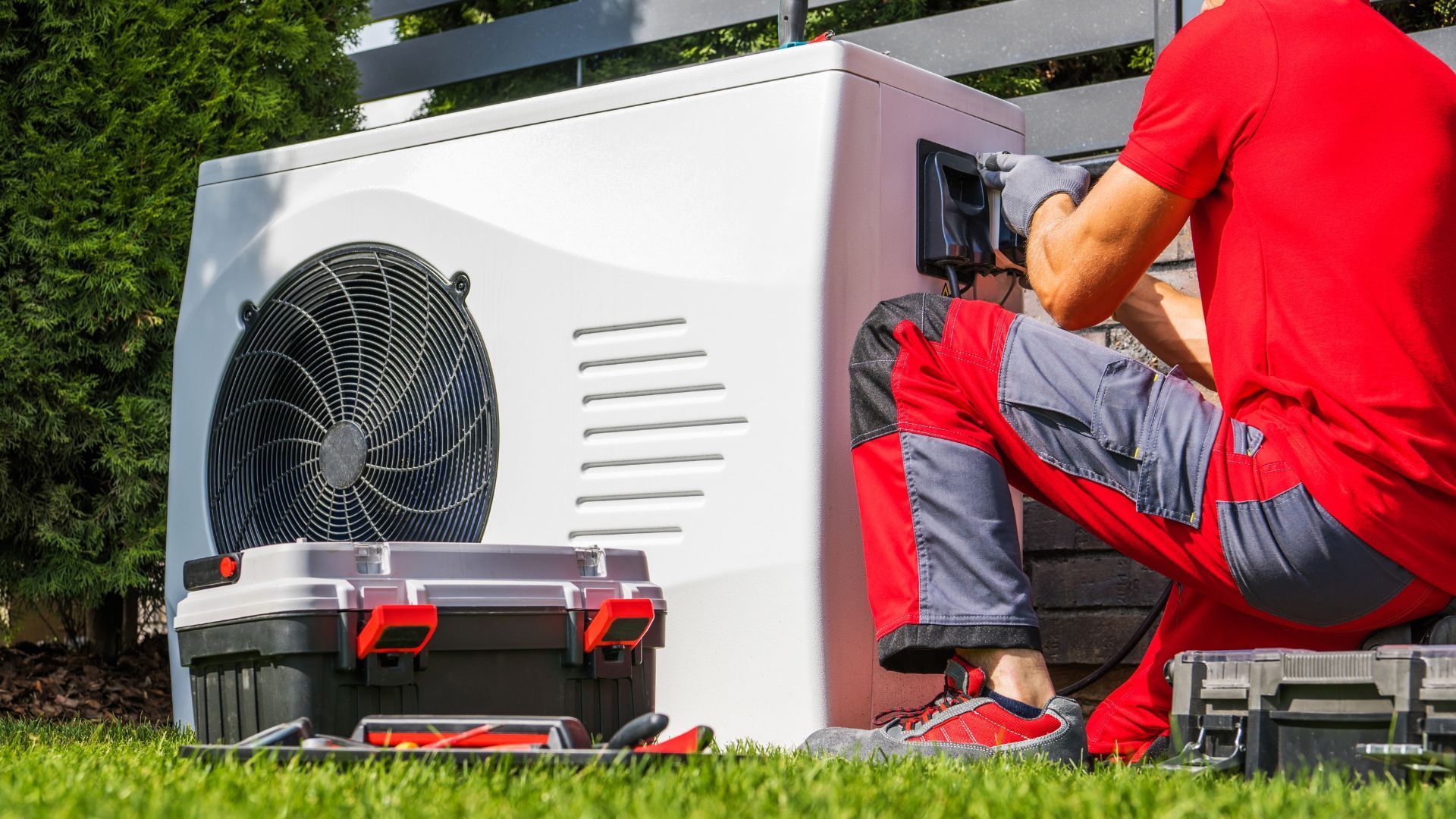
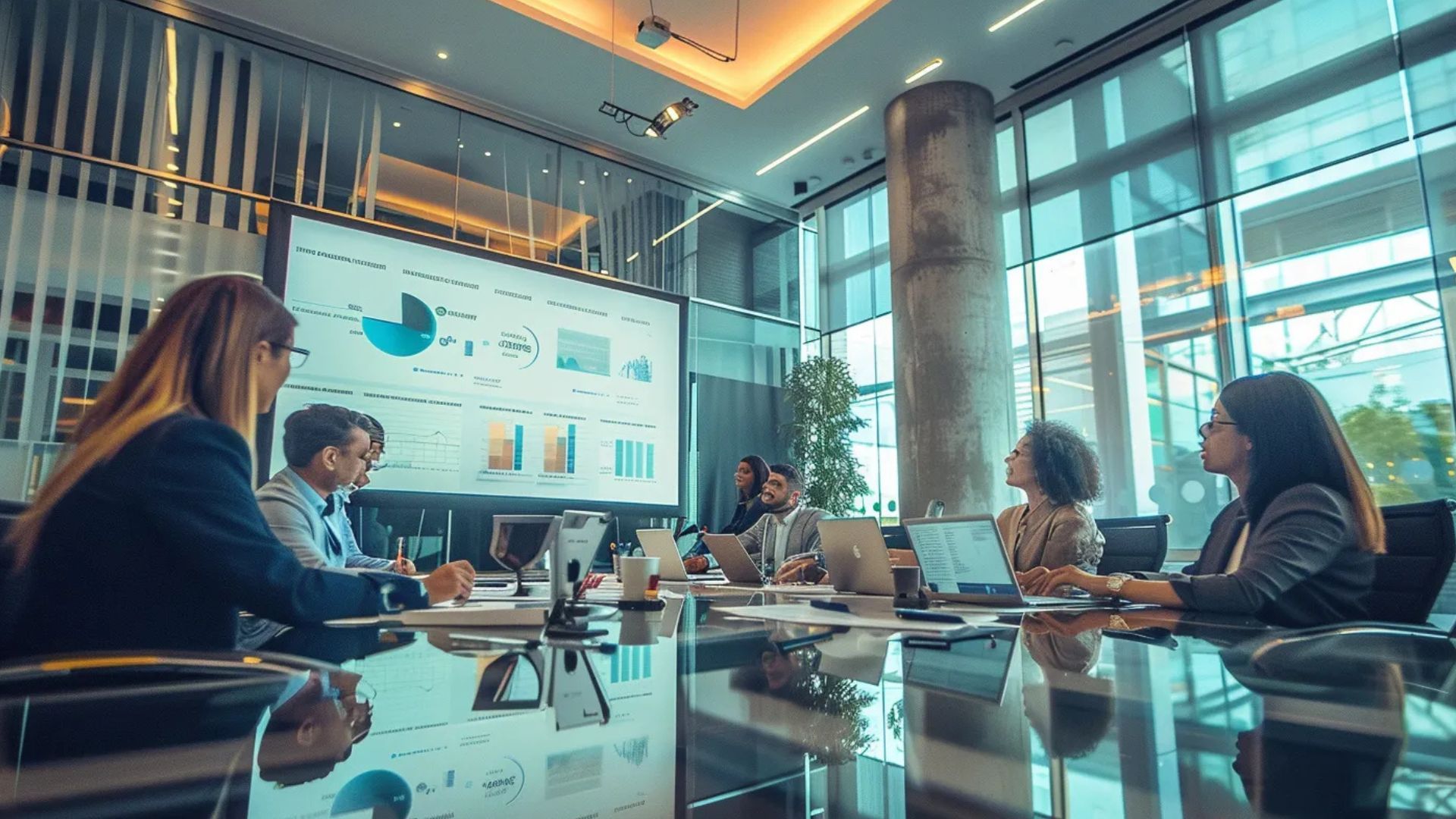