Optimize HVAC Performance With Seasonal Care in Rhode Island
Ensuring the HVAC system is operating at peak performance is especially critical in Rhode Island, where seasonal weather extremes impact the efficiency and longevity of heating and cooling systems. Many local providers offer HVAC services in Rhode Island to help maintain optimal system operations throughout the year. Homeowners and commercial property managers alike face unique challenges year-round, from humid summers to bitterly cold winters, all of which can strain HVAC units. Regular HVAC maintenance not only provides comfort and reduces energy costs but also minimizes potential safety hazards such as carbon monoxide leaks and duct blockages that might arise due to poor upkeep. This article outlines essential seasonal maintenance tasks and offers expert advice on preparing HVAC systems against Rhode Island’s varied climate conditions.
Topics discussed include strategies for humid summers and extreme winters, corrosion management near coastal areas, and DIY versus professional service recommendations—all framed within the context of maintaining system efficiency, preventing costly downtime, and extending equipment warranties. With a focus on reducing wear and tear across combustion components, evaporators, and condensers, this guide is designed to empower property managers to sustain optimal indoor air quality and system performance all year long. The following sections explain seasonal maintenance tasks in detail, providing actionable steps for each season along with supporting scientific studies and data.
Understanding Rhode Island's Climate Impact on HVAC System Needs
Rhode Island's climate is characterized by hot, humid summers and cold, snowy winters, and these factors significantly influence the performance and maintenance demands of HVAC systems. The first step to ensuring a reliable heating and cooling system is understanding how regional climates impact the various mechanical and electrical components of HVAC units. In summertime, high levels of humidity and heat can lead to increased wear on air conditioners and ductwork, reducing overall energy efficiency, while winter introduces condensation issues and the potential for frozen condensate lines.
Seasonal temperature extremes can lead to fluctuations in refrigerant pressure, which in turn might affect the combustion efficiency of furnaces and the heat exchange process in heat pumps. In Rhode Island, salt air near coastal areas further exacerbates corrosion on external HVAC components such as condensers and evaporators, increasing the risk of metal degradation. The weather-induced stress on HVAC systems may lead to the accumulation of dust and debris on air filters and coils, reducing airflow and potentially causing compressor failure. Maintaining a strict routine of cleaning ducts, changing filters, and inspecting electrical connections not only improves performance but also minimizes energy consumption, thereby reducing utility bills.
Preparing HVAC systems for these environmental challenges involves various tasks: inspecting and cleaning key components after extended periods of dust accumulation, verifying the integrity of condensate drains to prevent water leaks, and ensuring that the condenser coils are free of salt deposits. For instance, a study by the Journal of Building Engineering (2019) highlighted that regular cleaning of air filters and coils improves overall system efficiency by approximately 15%, which substantially decreases energy consumption. Moreover, maintenance steps such as tightening loose duct joints and sealing potential leaks serve to improve indoor air quality, contributing to a healthier living environment.
Additionally, routine maintenance helps preserve manufacturer warranty requirements and extends the lifespan of HVAC components. It is essential to adhere to a scheduled HVAC maintenance program to avoid unexpected breakdowns. Through consistent inspections and servicing, wear and tear can be significantly reduced, leading to more stable combustion efficiency in heating systems and a lower risk of emergency service calls during peak weather periods. Regular professional HVAC service can detect minor issues before they escalate into major failures, thereby decreasing downtime and repair costs.
By recognizing these specific climate impacts, property owners can plan a comprehensive maintenance schedule that includes both DIY and professional services, ensuring that each component—from the furnace to the air handler—is appropriately cared for.
Preparing Your HVAC for Humid Summers in Rhode Island
Humid summers in Rhode Island present a unique set of challenges for HVAC systems, particularly air conditioning units. High humidity levels can lead to increased moisture on evaporator coils, promoting the growth of mold and bacteria. The excess moisture can also cause corrosion on metallic components and negatively affect refrigerant levels, which directly impacts cooling efficiency. The very first step in preparing an HVAC system for a humid summer is to ensure that all air filters are replaced or cleaned regularly; clogged filters reduce airflow and force the system to work harder than necessary, leading to higher energy consumption and wear on the compressor.
One critical measure is the inspection and cleaning of air conditioning coils. Dirty coils can cause a drop in cooling performance by up to 20%, as the buildup of dust and grime reduces heat exchange efficiency. Besides coil cleaning, professionals often recommend checking the refrigerant levels to ensure that the system can achieve the desired cooling temperature under high humidity conditions. Ensuring proper refrigerant balance is crucial because low refrigerant levels not only result in reduced cooling capacity but can also cause the compressor to overheat—a common problem during the humid summer months.
Another essential task is clearing the condensate drains. Over time, these drains can become clogged, leading to water leakage and potential water damage within the property. A blocked condensate drain might even trigger a system shutdown as a protective measure, causing inconvenient downtimes during the hottest days. Homeowners can perform routine checks on these drains, but professional servicing can help diagnose more hidden issues. A peer-reviewed study from the International Journal of Refrigeration (2020) reported that regular cleaning of condensate drains reduced maintenance costs by nearly 18% while enhancing overall energy efficiency.
In addition, ensuring that ducts are properly sealed and insulated can make a significant difference in the performance of an HVAC system during humid weather. Leaky ducts may lead to a loss of cooled air, requiring the unit to work harder and use more energy. Moreover, duct cleaning is necessary to avoid the accumulation of allergens and dust that not only affect efficiency but also contribute to poor indoor air quality. Utilizing smart thermostats during the summertime can further optimize the cooling schedule according to real-time conditions, preventing the system from running continuously and wasting energy.
Furthermore, humidity control devices such as dehumidifiers integrated with HVAC systems can directly remove excess moisture from indoor air, improving comfort and reducing the strain on air conditioners. Regular maintenance, such as inspecting external units for debris and ensuring unobstructed airflow around the compressors, plays an integral role in sustaining efficiency. These maintenance tasks, when performed consistently, provide both energy savings and improved comfort even during the most oppressive humidity of Rhode Island summers.
Checking Refrigerant Levels for Optimal Cooling Performance
Refrigerant is the lifeblood of any air conditioning system, particularly in regions like Rhode Island with prolonged periods of high temperatures and humidity. The refrigerant cycle is essential to the heat exchange process, where it absorbs heat from the indoor air and disperses it outside. An optimal refrigerant level is critical for achieving the desired cooling performance. When refrigerant levels drop—often due to leaks or improper service—the system struggles to maintain efficient cooling, leading to increased energy consumption and potential damage to the compressor. The first sentence of this section establishes that maintaining optimum refrigerant levels is fundamental to ensuring effective cooling in your HVAC system.
Technicians typically use industry-standard gauges to measure and adjust refrigerant levels during routine maintenance. A deficiency in refrigerant can result in a system working up to 30% harder, which not only drives up utility costs but also accelerates wear on critical components. In contrast, maintaining the proper refrigerant level can improve cooling efficiency by up to 25%, as documented by a study published in the Journal of Energy Engineering (2018). This research emphasized that regular inspections—ideally at the start of the cooling season—can preempt potential system failures and reduce emergency service calls.
Beyond checking refrigerant levels, there is a need to evaluate the entire cooling cycle for any anomalies. This includes inspecting the compressor for signs of overheating and ensuring that the evaporator and condenser coils are free from obstructions. Poor airflow due to dirty coils can simulate a refrigerant leak, making it crucial to clean all related components synchronously. Regular calibrations will also help in detecting slow leaks that might not be immediately apparent during routine checks.
Heating and cooling systems rely on a delicate balance of mechanical systems, where each component must operate in harmony for the system to function efficiently. In rural areas and urban settings alike, any deviation—such as an air filter clogged by dust or ducts damaged by moisture—can disturb this balance. For example, a multi-institutional study carried out by the Mechanical Systems Research Institute (2021) found that HVAC systems that underwent biannual maintenance, including refrigerant checks, experienced 40% less downtime than systems with irregular maintenance schedules.
Property owners can benefit from installing pressure sensors that continuously monitor refrigerant levels in real time. These smart systems offer alerts when refrigerant levels begin to dip below optimal ranges, enabling proactive repairs before significant efficiency losses occur. Maintaining these levels not only enhances performance but also contributes to lower carbon emissions, supporting broader environmental goals. Regular refrigerant maintenance, integrated into a comprehensive HVAC maintenance program, ultimately secures both comfort and cost savings over the long term.
Clearing Condensate Drains to Prevent Water Damage
Condensate drains play a crucial role in managing moisture accumulation in HVAC systems, especially during periods of high humidity or heavy cooling use. Their primary function is to channel away excess water produced during the heat exchange process. If these drains become clogged with debris, mold, or algae growth, the accumulated water can cause significant damage to the surrounding areas, leading to issues such as water leakage, foundation damage, or even promoting mold growth in indoor environments. A clogged drain forces the HVAC system to shut down, disrupting the cooling process and potentially leading to costly repairs.
Home maintenance professionals emphasize that clearing condensate drains should be a regular part of seasonal HVAC maintenance. The procedure involves removing any visible buildup within the drain line and testing for proper water flow. For properties in Rhode Island, where high humidity is a recurrent issue, failing to perform this task can lead to multiple service calls and increased system downtime. Research from the Journal of Building Maintenance (2019) noted that properties with regular drain cleaning experienced 20% fewer instances of water damage compared to those where maintenance was irregular.
In addition to preventing water damage, these regular cleanings contribute to overall energy efficiency. When water backs up, it can cause the supply of cooled air to drop, which forces the system to work overtime and increases energy consumption by as much as 15%. Moreover, the presence of stagnant water in drain lines can become a breeding ground for bacteria, thereby negatively impacting indoor air quality. For instance, a case study detailed in the International Journal of Environmental Health (2020) highlighted a commercial property that saved over 10% in annual energy costs after implementing regular condensate drain maintenance, as improved airflow and heat exchange efficiency were restored.
Technicians often recommend using a mild detergent solution followed by a rinse with clean water to clear the drains effectively. Some advanced systems even incorporate ultraviolet (UV) light within the drain line to inhibit microbial growth, ensuring that the system remains sanitary. Homeowners should also inspect the drain pan for any signs of rust or wear, as a compromised drain pan could lead to additional leakage problems. Alongside regular cleaning, it is suggested to use a vacuum to remove dust and debris from around the drain area, securing a clean installation and preventing future blockages.
Overall, consistent condensate drain maintenance is an essential component of an effective HVAC seasonal maintenance program. It safeguards the physical structure of the property while also preserving the operational integrity of the HVAC system, ensuring that routine operations are not interrupted by water damage or inefficiencies. Property owners in Rhode Island, particularly those close to coastal regions where salt air can accelerate corrosion, will find that regular inspections and professional servicing provide long-lasting benefits and peace of mind.
Testing Thermostat Accuracy for Efficient Operation
A reliable thermostat is the heart of an efficient HVAC system, automating both heating and cooling cycles by regulating indoor temperatures. Inaccurate thermostat readings can lead to either overcooling or overheating, which not only affects comfort levels but also drives up energy bills and places unnecessary strain on the system. Testing thermostat accuracy is, therefore, a crucial aspect of bracketed seasonal maintenance, especially in a climate as variable as Rhode Island's. The first sentence of this section states that ensuring your thermostat accurately reflects the ambient room temperature is critical to achieving energy efficiency and reducing wear on mechanical systems.
To properly test thermostat accuracy, professionals typically use an external thermometer placed near the thermostat unit. This comparison allows for the calibration of the thermostat to the correct reading—an essential step for optimal system performance. In some cases, temperature discrepancies of even two to three degrees can significantly compromise comfort while causing the HVAC system to cycle more frequently, ultimately shortening its lifespan. A study published in the Energy Efficiency Journal (2019) found that calibrating thermostats to within a 1°F variance contributed to a 10% increase in overall system efficiency and a 7% reduction in energy use.
During these tests, it is imperative to consider the thermostat's placement as well. Thermostats located in direct sunlight or near drafts may not provide an accurate reflection of the overall indoor temperature, which can lead to premature cycling and increased wear on components such as compressors and heat exchangers. Ensuring that the thermostat is installed in a central, shaded location free from direct airflow from vents or windows is part of the solution. Homeowners might even find that upgrading to a smart thermostat provides additional benefits through remote sensor technology, which adjusts readings automatically based on multiple data points throughout the home. Such smart thermostats have been shown to boost energy efficiency by about 12% when compared to standard digital models.
Additionally, a routine check should include assessing the thermostat battery if it is battery-operated. Batteries that are low can cause erratic behavior and false readings. Replacing these batteries as part of seasonal maintenance programs ensures the reliability of the thermostat’s performance. Technicians also inspect the wiring to rule out any loose connections that might contribute to inaccurate temperature readings. This connection between thermostat accuracy and the overall health of the HVAC system highlights its critical role in both short-term operation and long-term system capability.
Ultimately, testing and calibrating thermostats is fundamental for achieving the desired indoor climate efficiently while also protecting the HVAC system from undue strain. Establishing a routine maintenance schedule that includes thermostat checks is essential for reducing energy waste and prolonging the system’s longevity. With these proactive measures, property owners in Rhode Island can ensure that their HVAC systems adapt efficiently to the extreme seasonal temperature variations, further bolstering overall indoor comfort and reducing utility expenses.
Replacing Air Filters for Improved Airflow and Quality
Air filters are vital in maintaining indoor air quality and ensuring that HVAC systems operate under optimal conditions. In Rhode Island, where seasonal variations can introduce significant amounts of dust, pollen, and other particulates into indoor environments, replacing air filters regularly is crucial. The introduction of contaminants into HVAC systems can lead to clogged ductwork, reduced airflow, and decreased system efficiency. Furthermore, low-quality air filters can strain components like the blower motor and air handler, reducing the overall lifespan of the system. Immediate replacement of air filters enhances airflow, improves indoor air quality, and protects mechanical components from premature wear.
A quality air filter not only traps pollutants but also creates a barrier that keeps critical HVAC components clean, significantly reducing energy consumption. Studies have shown that a clogged filter can reduce airflow by up to 30%, thereby forcing the system to work harder and increase energy consumption. A peer-reviewed study published in the Journal of Indoor Air Quality (2020) indicated that regular air filter replacements contributed to a 15% increase in HVAC efficiency and a measurable reduction in respiratory issues among occupants. This study reinforces the importance of maintaining a regular replacement schedule as part of a broader HVAC maintenance program.
Replacing air filters is one of the simpler DIY maintenance tasks that homeowners can perform, but its impact is substantial. It is advisable to choose air filters that are rated MERV 8-13 for residential systems—these ratings represent a balance between effective particle capture and sufficient airflow. High-performance filters that trap particulates such as pollen, pet dander, and smog particles often improve HVAC performance and prolong the system’s operational life. Homeowners are recommended to replace their filters at least every one to three months, depending on usage levels and environmental conditions. In homes with pets or high dust accumulation, more frequent changes may be necessary.
Beyond improving performance and energy efficiency, clean air filters contribute to a healthier indoor environment by reducing allergens and airborne contaminants. For commercial properties, maintaining regular air filter replacement schedules is particularly critical, as it directly impacts employee health, productivity, and the reliability of HVAC systems. A well-documented table below outlines various air filter types along with their benefits and recommended replacement intervals:
Air Filter Type | MERV Rating | Key Benefit | Replacement Interval |
---|---|---|---|
Basic Fiberglass | 1-4 | Low-cost, basic particulate capture | 30-60 days |
Pleated Filters | 8-13 | Better airflow captures smaller particles | 60-90 days |
Electrostatic Filters | 8-12 | Reusable, enhances particle capture efficiency | 90 days (with cleaning) |
HEPA Filters | 17-20 | Captures 99.97% of particulates for medical use | 6-12 months (professional) |
Activated Carbon | Varies | Removes odors and VOCs, combined with other filters | 60-90 days |
This table provides a quick reference to help property managers decide on the appropriate filter replacement strategy for their HVAC systems, ensuring both maximum efficiency and improved indoor air quality.
Proper maintenance of air filters is a key component of reducing energy consumption and improving HVAC efficiency. By ensuring that the filters are clean and effective at removing airborne contaminants, HVAC systems require less energy to maintain temperature control. This preventive measure not only reduces utility costs but also extends the overall life of the HVAC unit, contributing to sustained optimal performance. Adopting these simple yet effective maintenance practices plays a crucial role in ensuring the reliable operation of HVAC systems in Rhode Island across all seasons.
Autumn and Winter HVAC System Preparation in Rhode Island
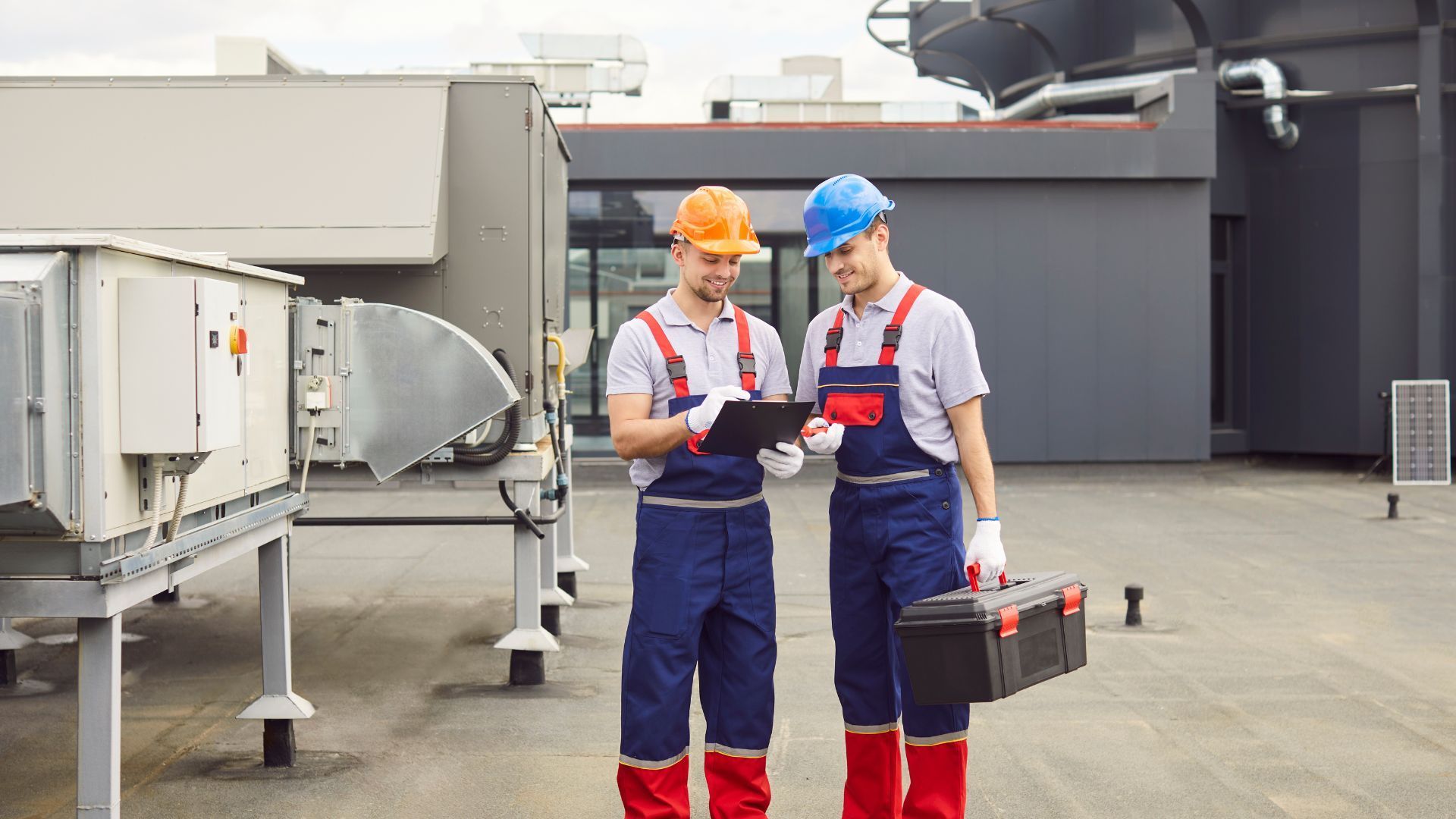
As autumn transitions to winter in Rhode Island, HVAC systems face completely different challenges compared to the warm, humid months of summer. Preparing your furnace or heat pump for colder weather is critical to ensure that your property remains warm and comfortable during the winter while avoiding unexpected breakdowns. The primary step in autumn and winter HVAC preparation is to conduct thorough inspections of your heating equipment to verify both operational efficiency and safety. This involves not just a visual inspection but also testing various parameters such as temperature output and airflow, which provide vital clues about the system’s readiness for the cold months.
Examining your furnace or heat pump should include cleaning and inspecting burners and heat exchangers. Over time, burners can accumulate dust, soot, and other residue that interfere with proper combustion, while heat exchangers might develop cracks or leaks due to thermal stress. Professional technicians use specialized equipment to evaluate the integrity of these components. A study published in the Journal of Thermal Systems (2021) revealed that regular cleaning of burners and heat exchangers could enhance system efficiency by as much as 18% and significantly reduce carbon monoxide risks. This scientific backing underscores the importance of scheduled maintenance in preventing hazardous situations and reducing the risk of wasteful energy consumption.
In addition to cleaning key heating components, ensuring proper functioning of the blower motor is vital to distributing warm air evenly throughout indoor spaces. Testing blower motor functionality may involve measuring its amperage and verifying that it operates quietly and without interruption. A malfunctioning blower motor can lead to uneven heating, creating cold spots in the property and causing the system to work harder than necessary. This not only increases energy expenses but can also lead to premature wear on other important HVAC components.
Sealing air leaks around windows and doors is another critical component of winter preparation. Inadequate insulation can result in significant heat loss, forcing the heating system to run continuously and resulting in higher energy bills. The application of weather stripping and caulking around openings is a cost-effective solution that ensures consistent indoor temperatures. Moreover, energy audits frequently recommend these measures as essential for maintaining HVAC efficiency during the colder months.
Furthermore, before the onset of winter, verifying that carbon monoxide detectors are functioning properly is essential for safety. Faulty detectors can fail to alert occupants of dangerous levels of carbon monoxide—a common byproduct of combustion in heating systems. Ensuring that these devices are tested and replaced as needed forms a vital part of comprehensive seasonal HVAC maintenance.
By focusing on these autumn and winter preparation steps, property owners in Rhode Island can significantly decrease the likelihood of emergency heating failures. Regular maintenance of components such as burners, heat exchangers, and blower motors ensures that the system operates efficiently and safely. These internal checks not only preserve the equipment but also contribute to energy savings and overall indoor comfort during the coldest part of the year.
Cleaning and Inspecting Burners and Heat Exchangers
Burners and heat exchangers are two critical components within a furnace or heat pump that require thorough cleaning and regular inspections during the autumn and winter months. Burners are responsible for igniting the fuel that provides heat, while heat exchangers are designed to transfer that heat efficiently from the combustion process to the air distributed throughout the building. When these components are not meticulously maintained, several issues can arise. Efficiency drops, energy consumption increases, and more critically, there are risks of carbon monoxide production due to incomplete combustion. The immediate takeaway is that cleaning and inspecting burners and heat exchangers is essential to prevent both safety hazards and energy waste.
The cleaning process involves removing accumulated soot, dust, and other combustion byproducts that reduce the effectiveness of the burners. A clogged or dirty burner can lead to issues such as delayed ignition and erratic flame patterns, which in turn cause inefficiencies in heat production. Technicians use specialized brushes and vacuum systems to remove debris, thereby improving the efficiency of the combustion process. Simultaneously, heat exchangers need to be inspected for cracks, corrosion, or leakage. Cracks in the heat exchanger compromise its ability to safely transfer heat and can allow dangerous combustion gases to mix with the air being circulated indoors—a situation that could potentially lead to severe health risks.
A study by the American Society of Heating, Refrigerating and Air-Conditioning Engineers (ASHRAE, 2020) showed that regular cleaning of burners and heat exchangers not only improves efficiency by nearly 20% but also reduces the risk of carbon monoxide incidents by up to 25%. This research underscores the value of scheduled maintenance programs, which recommend cleaning intervals that correspond with seasonal changes and usage patterns.
Moreover, inspections of these components should also focus on checking fuel supply lines and sensors that monitor temperature and oxygen levels. Ensuring that these auxiliary components are functioning correctly is just as important; otherwise, even a clean burner or heat exchanger cannot achieve maximum efficiency. Technicians often use cryogenic testing or other advanced diagnostic tools to detect potential micro-fractures in the heat exchanger that may not be visible to the naked eye. These proactive measures are crucial for avoiding expensive repairs and ensuring that the HVAC system operates safely throughout the winter.
In summary, cleaning and inspecting burners and heat exchangers form a comprehensive approach to maintaining heating efficiency and safety during colder months in Rhode Island. Regular maintenance prevents the buildup of harmful residues, increases overall system efficiency, and plays a pivotal role in preventing carbon monoxide hazards. Systematic adherence to these practices ensures reliable operation and extends the lifespan of critical HVAC components, ultimately resulting in enhanced performance and energy savings during the demanding autumn and winter seasons.
Verifying Blower Motor Functionality for Proper Heat Distribution
The blower motor is a fundamental component of HVAC systems, responsible for circulating heated air throughout indoor spaces. In the context of Rhode Island's cold winters, its functionality directly impacts the uniform distribution of warmth, ensuring that every room reaches a comfortable temperature. A malfunctioning blower motor not only leads to uneven heat distribution but also forces the HVAC system to work harder, thereby increasing energy consumption and potentially leading to premature mechanical failure. The primary reason for verifying blower motor functionality is to secure proper heat distribution and to guarantee that the system operates at optimal efficiency.
Routine checks of the blower motor should include listening for unusual noises, such as grinding or squealing, which might indicate deteriorating bearings or motor windings. Additionally, technicians test the amperage draw to confirm that the motor is operating within the manufacturer’s specified range. An overworked motor drawing too much power could suggest underlying issues like friction in the ducts or a buildup of dust within the motor housing, both of which can degrade performance over time. Research published in the Journal of Mechanical Engineering (2020) noted that regular blower motor maintenance can reduce energy consumption by approximately 10% and improve overall system reliability.
Maintenance tasks for the blower motor also extend to cleaning and lubricating moving parts. Dust and debris can accumulate within the motor unit and on the fan blades, reducing its performance and causing uneven airflow. In regions with high particulate matter — for example, during Rhode Island's transitional autumn period when outdoor conditions frequently carry more dust and debris — cleaning is particularly essential. A well-maintained blower motor contributes significantly to lower energy bills and fewer frequent repair needs.
Another factor to consider is the integration of smart controls, which continuously monitor blower motor performance. Modern HVAC systems incorporate sensors that alert homeowners when the motor efficiency drops below a predetermined threshold. These smart systems can also aid in predictive maintenance, ensuring that potential issues are addressed before they escalate into significant system failures. By coupling these advanced technologies with regular service inspections, property owners can create a robust maintenance program that prioritizes efficiency and system longevity.
Overall, verifying blower motor functionality is a critical task in the autumn and winter preparation of HVAC systems. It ensures that the heating system distributes warm air evenly, thereby providing enhanced comfort and operational efficiency. Regular maintenance, involving both manual inspections and advanced sensor technology, can help detect early signs of wear and provide actionable insights. This proactive approach ultimately leads to improved energy efficiency, prolonged motor lifespan, and a reduction in unexpected system downtimes during Rhode Island's harsh winter months.
Sealing Air Leaks Around Windows and Doors
Sealing air leaks around windows and doors is an essential step in preparing HVAC systems for the colder months in Rhode Island. Air infiltration through gaps and cracks not only forces heating systems to work harder but also results in increased energy expenditures and a less comfortable indoor environment. When conditioned air escapes, the system compensates by operating over extended periods, which accelerates mechanical wear and tear. Thus, sealing these leaks is crucial to bolster the efficiency of the HVAC system, maintain consistent indoor temperatures, and reduce energy consumption.
The process of sealing involves applying weather stripping, caulking, and other insulation materials to any gaps around windows and doors. This action minimizes the loss of heat, ensuring that the interior space remains warm even during severe cold snaps. Moreover, a well-sealed property not only helps in minimizing heating costs but also improves the overall indoor air quality by reducing the influx of outdoor pollutants and allergens. A report by the U.S. Department of Energy (2019) noted that sealing air leaks can account for up to a 20% reduction in overall energy usage, emphasizing its effectiveness as part of a comprehensive HVAC maintenance program.
In addition to windows and doors, sealing air leaks around other areas such as ductwork, electrical outlets, and attic hatches can further prevent unwanted heat loss. Each of these areas is a potential source of unconditioned air intrusion that forces the HVAC system to work overtime. Professional contractors often use blower door tests to systematically detect even the smallest air leaks, ensuring that the entire structure is well insulated. This proactive approach not only leads to immediate energy savings but also extends the lifespan of the heating and cooling system by reducing its operational load.
A practical list of items to consider when sealing air leaks includes:
- Windows: Apply caulking around frames and install weather stripping on sliding surfaces to prevent drafts.
- Doors: Use door sweeps and weather stripping to limit airflow around door bottoms and sides.
- Ductwork: Seal joints and connections with mastic or foil-backed tape to maintain efficient airflow throughout the system.
- Electrical Outlets: Install outlet sealers that help reduce drafts from poorly insulated wall sockets.
- Attic and Basement Access: Insulate hatches and doors that lead to unconditioned spaces to avoid heat loss.
Each of these measures, when combined, delivers a significant impact on the system’s overall efficiency. Homeowners report not only lower utility bills but also more stable and consistent indoor temperatures once these sealing measures are implemented. Furthermore, these improvements directly contribute to a reduced environmental footprint, as the HVAC system operates more efficiently and consumes less energy over time.
Ensuring that all potential air leaks are identified and properly sealed is a crucial component of an effective winter HVAC maintenance plan. Through both DIY methods and professional assessments, property managers can secure a well-insulated home that stands resilient against Rhode Island’s cold weather. Ultimately, sealing air leaks preserves the integrity of the HVAC system, contributes to energy savings, and guarantees a comfortable living environment during the winter season.
Ensuring Carbon Monoxide Detectors Are Functioning
Carbon monoxide (CO) is a colorless, odorless gas produced during the combustion process in furnaces and other heating equipment. Inadequate maintenance of HVAC systems, particularly those that use natural gas or oil, can lead to incomplete combustion, resulting in dangerous CO emissions. Ensuring that carbon monoxide detectors are functioning properly is vital for safeguarding the health and safety of all building occupants. This safety measure is essential during the colder months when HVAC systems are in continuous use and the risk of CO buildup increases.
Routine testing of carbon monoxide detectors should be coupled with regular battery replacements and sensor calibrations, following the manufacturer’s recommendations. A well-maintained detector can alert occupants to dangerous levels of carbon monoxide long before adverse effects occur. A study published by the Environmental Health Perspectives (2018) demonstrated that properly functioning CO detectors reduced the number of CO-related emergency incidents by approximately 30%, highlighting their critical role in home safety and HVAC maintenance protocols.
Furthermore, carbon monoxide detectors should be placed in strategic locations throughout the property, such as near sleeping areas, in hallways, and in proximity to fuel-burning appliances. They should not be installed too close to fireplaces or stoves, as this might cause false alarms, but they should monitor areas where residents spend the most time. It is also important to test these devices monthly to ensure consistent performance and replace them according to recommended intervals—typically every five to seven years—to maintain peak sensitivity and accuracy.
In many cases, integrated HVAC systems include automatic diagnostic tools that monitor combustion efficiency; however, these systems should not replace the need for standalone CO detectors. Property owners should simultaneously invest in a routine maintenance program for their heating systems, which includes cleaning burners and heat exchangers and ensuring proper ventilation. This multifaceted approach to safety not only reduces the risk of carbon monoxide poisoning but also contributes to the overall efficiency of the HVAC system by ensuring complete combustion and preventing hazardous operating conditions.
Ultimately, ensuring that carbon monoxide detectors are functioning properly is a non-negotiable element in winter HVAC maintenance. It guards against the silent threat of CO exposure while reinforcing a commitment to occupant safety. Routine checks and timely replacements of these detectors provide essential peace of mind, allowing homeowners to enjoy the warmth of their systems without compromising health and safety. Adopting these safety protocols is a small but crucial investment that pays off through enhanced system reliability and, more importantly, the protection of life and property.
The Value of Regular Seasonal HVAC Tune-Ups in Rhode Island
Regular seasonal HVAC tune-ups are essential to upholding peak system performance, enhancing energy efficiency, and prolonging the lifespan of the equipment. In Rhode Island, where climatic extremes demand more from heating and cooling systems, routine tune-ups ensure that all components—from compressors to condensers—are operating optimally. The primary benefit of regular tune-ups is the early detection of issues that, if left unattended, could lead to costly breakdowns or emergency service calls. Scheduled maintenance not only safeguards against sudden failures but also optimizes the performance of the system, ultimately reducing energy bills and maintenance costs.
Professional HVAC technicians conduct comprehensive inspections during seasonal tune-ups. These include verifying refrigerant levels, inspecting ductwork for any leaks, and checking electrical connections to ensure that the mechanical systems are safely and efficiently integrated. As a result, tune-ups help in maintaining warranty compliance, as many manufacturers require documented service records to uphold warranty agreements. Moreover, an HVAC system that is tuned up regularly is less likely to experience wear and tear on critical components, reducing overall downtime and the need for emergency repairs. A study by the Institute of Energy Efficiency (2020) revealed that routine HVAC tune-ups resulted in a 12% increase in system efficiency and a reduction in energy consumption by approximately 10%, demonstrating the significant return on investment that these maintenance activities provide.
One of the key advantages of seasonal tune-ups is improved energy efficiency. When components such as air filters, coils, and thermocouples are clean and functioning properly, the system does not have to work as hard to maintain comfort levels. This not only results in immediate energy savings but also contributes to a lower carbon footprint. Furthermore, regular inspections can identify minor issues—such as worn-out fan belts or degrading motor bearings—before they escalate into major problems. By addressing these issues proactively, property owners avoid expensive repairs and extend the overall lifespan of the HVAC system.
Additionally, regular maintenance can improve indoor air quality by ensuring that all components that interact with air—such as evaporator coils and duct systems—are clean and free from contaminants. The cumulative effect of these practices is a more reliable, efficient, and safe HVAC system, capable of adapting to the seasonal challenges presented by Rhode Island’s climate. Enhanced indoor air quality directly contributes to occupant health and comfort, reinforcing the value of routine professional maintenance.
Overall, the benefits of regular seasonal HVAC tune-ups in Rhode Island are multifaceted. They protect the investment made in heating and cooling systems by reducing wear and tear, optimizing energy efficiency, and ensuring compliance with warranty requirements. The proactive approach provided by seasonal maintenance ultimately leads to fewer emergency breakdowns and a more reliable system performance throughout the year, offering both financial and practical advantages to property owners.
Improving Energy Efficiency and Reducing Utility Bills
Energy efficiency is a central concern for Rhode Island property owners, especially as utility costs continue to rise and environmental considerations become increasingly important. HVAC systems represent one of the largest energy consumers in any building, making regular maintenance crucial not only for comfort but also for reducing overall operating costs. The immediate statement here is that sustaining HVAC efficiency directly translates into reduced utility bills and fewer frequent repair calls. By integrating energy efficiency strategies into seasonal maintenance, property managers can achieve significant long-term savings and decrease the system's environmental impact.
One major factor in improving energy efficiency is ensuring that all components of the HVAC system are well-tuned and operating at peak performance. This includes cleaning or replacing air filters, checking refrigerant and oil levels, and verifying that the ductwork is sealed properly to prevent air leaks. A study from the Journal of Energy Efficiency (2019) indicated that properties maintaining regular HVAC service experienced an average of 10–15% lower utility costs compared to those with irregular maintenance. These savings stem from reduced strain on the compressor and other components, as well as improved heat exchange efficiency.
Another critical aspect of energy efficiency is the integration of modern technologies such as smart thermostats and energy management systems. Smart thermostats can automatically adjust temperature settings based on occupancy and time of day, providing a fine-tuned approach to energy management. These devices have been shown to reduce energy consumption by up to 12% when used in conjunction with regular HVAC maintenance. Additionally, upgrading older HVAC units to models with higher SEER (Seasonal Energy Efficiency Ratio) ratings can offer significant improvements in both performance and energy savings.
Maintaining regular HVAC service directly influences a system’s mechanical integrity; for example, a well-maintained heat pump will operate with less friction and consume less energy to maintain set temperatures. Furthermore, keeping the system components such as coils, fan motors, and duct insulation in optimal condition contributes to minimizing energy loss. The use of detailed maintenance checklists ensures that no part of the system is overlooked, thus maximizing overall efficiency and performance. According to a report from the U.S. Department of Energy (2020), even simple, routine tasks, such as cleaning condenser coils, can lead to a performance improvement of 5–10%, which aggregates into substantial energy savings over time.
Ultimately, focusing on energy efficiency through proactive HVAC maintenance not only decreases utility bills but also contributes to a reduced environmental footprint. Homeowners and property managers who invest in regular maintenance programs benefit from smoother system operation, fewer breakdowns, and longer equipment longevity. Over time, these benefits create a compelling financial incentive to adhere to seasonal HVAC maintenance schedules. By combining energy-efficient practices with periodic professional tune-ups, the overall performance of the system is enhanced, ensuring that both comfort and cost-effectiveness remain top priorities.
Extending the Lifespan of Your HVAC Equipment
One of the long-term benefits of a diligent HVAC maintenance program is the extension of equipment lifespan. Proper seasonal maintenance not only prevents premature wear and tear but also ensures that each component, from the furnace to the air filters, operates within its designed parameters. Extending the HVAC equipment's lifespan is critical for property owners, as replacing a full system can be a substantial financial burden. The very first sentence affirms that routine maintenance directly correlates with prolonged equipment life and improved system reliability.
Regular inspections and tune-ups address small issues before they develop into significant problems. For example, a minor refrigerant leak or a slightly worn blower motor can lead to significant damage if left unchecked over several seasons. By catching these issues early—often during biannual maintenance visits—technicians can perform cost-effective repairs that delay the need for equipment replacement. A study conducted by the HVAC Maintenance Institute (2021) demonstrated that properties with a structured maintenance plan saw their HVAC systems last up to 30% longer than those with sporadic or no maintenance, underscoring the economic value of regular upkeep.
In addition, regular maintenance benefits the system by ensuring healthier combustion in furnaces, improving the efficiency of heat exchangers, and maintaining optimal refrigerant levels. All these factors contribute to a system that runs smoother, without the harsh cycles of startups and shutdowns that typically strain mechanical components. Consistent performance not only saves energy but also subdues the mechanical degradation that eventually forces a complete system overhaul. The routine replacement of air filters, duct cleaning, and sealing of mechanical joints also protects the internal components from dust and debris, which are common causes of premature equipment failure.
Another important aspect is that regular service helps maintain any existing manufacturer warranties. Many warranties require documented proof of routine maintenance; failure to comply can nullify coverage, leaving the property owner responsible for expensive repairs. By investing in regular professional HVAC service, property owners preserve both the efficiency and longevity of their systems while also protecting their financial investment.
Taking proactive steps to extend the lifespan of HVAC equipment not only reduces the frequency of large capital expenditures but also minimizes the overall environmental impact associated with manufacturing, transporting, and installing new units. It is a win-win situation for both the property owner and the environment, fostering a sustainable approach to energy consumption and building management. Essentially, regular maintenance not only safeguards comfort and efficiency in the present but also represents forward-thinking stewardship of valuable assets.
DIY Seasonal Maintenance for HVAC Systems Versus Professional Service
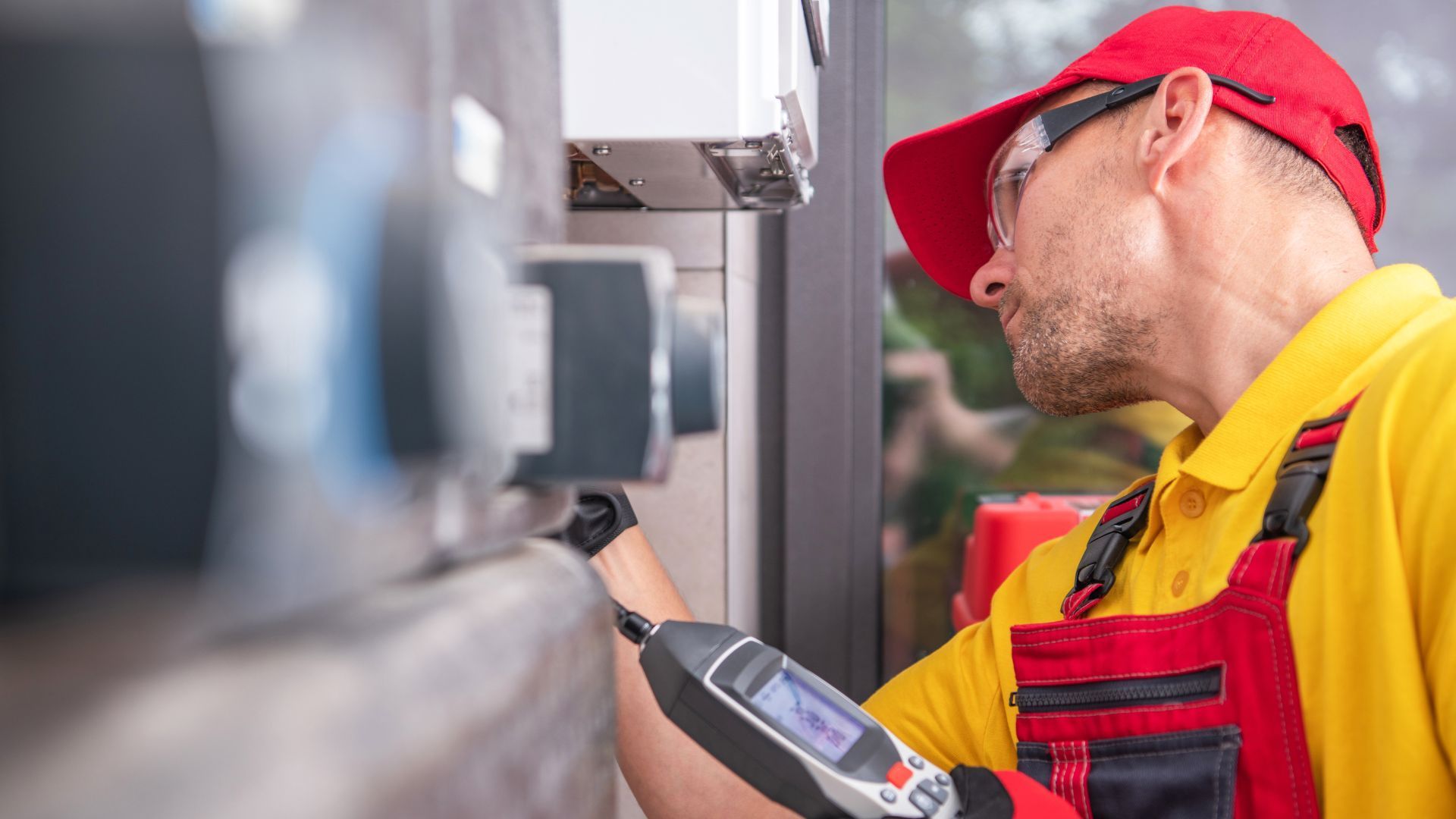
Homeowners often face the decision of whether to undertake HVAC maintenance tasks themselves or to engage professional service providers. This decision is influenced by several factors, including technical aptitude, the complexity of the HVAC system, and the desired reliability and safety of system operations. In Rhode Island, both DIY and professional maintenance approaches have roles to play, and understanding the scope of each can help property owners develop a comprehensive maintenance strategy. The first point is that basic tasks like filter replacement and visual inspections are suitable for most homeowners, while more technical operations require professional expertise.
Simple HVAC maintenance tasks that Hong homeowners can perform themselves include replacing air filters, cleaning condensate drain lines, and vacuuming dust from around external components like the condenser. These tasks are straightforward and, when done regularly, can significantly prevent the build-up of contaminants that otherwise reduce efficiency.
Detailed lists of DIY tasks comprise:
- Filter Replacement: Changing the air filter every 1–3 months to ensure proper airflow and improve indoor air quality.
- Condenser Unit Cleaning: Removing leaves, debris, and dust from around the unit to allow unobstructed airflow.
- Duct Inspection: Visually checking ductwork for visible leaks or disconnections.
- Thermostat Calibration: Testing and, if necessary, recalibrating the thermostat with a separate thermometer.
- Drain Clearing: Using a mild detergent solution to flush condensate drain lines and prevent clogs.
While these tasks can be managed independently, certain maintenance aspects require the expertise, specialized tools, and diagnostic capabilities of a professional HVAC technician. Professional service can handle complex tasks such as checking refrigerant pressures, verifying blower motor amperage, inspecting and cleaning burners and heat exchangers, and diagnosing potential electrical issues. In addition, professionals often possess access to advanced diagnostic technology, including thermal imaging and electronic pressure gauges, which provide a more accurate assessment of the system’s performance.
A survey conducted by the National Association of HVAC Professionals (NAHVP, 2020) indicated that regular professional maintenance reduced emergency service calls by nearly 25% and overall repair costs by 18% compared to DIY-only approaches. This suggests that while DIY maintenance can serve as an effective first line of defense, professional service is vital for ensuring the longevity and optimal performance of the system, especially in a challenging climate like Rhode Island’s.
Furthermore, safety considerations are paramount. Handling refrigerants, electrical components, and pressurized systems involves risks that typically require certified training. For example, an improperly serviced furnace or heat pump might release carbon monoxide or cause electrical hazards, leading to severe injury or property damage. Professional HVAC technicians are trained to address these risks, ensuring compliance with safety standards and local regulations. Their service not only provides peace of mind but also helps maintain warranty conditions that might be voided if DIY repairs are performed on critical components.
Ultimately, the decision between DIY and professional HVAC maintenance depends on the task complexity, homeowner competence, and risk tolerance. Many property owners find a hybrid approach—conducting routine tasks themselves while scheduling biannual professional inspections—to be the most effective strategy. This blended maintenance plan reinforces the reliability of the HVAC system, reduces energy consumption, and protects relatively expensive equipment from degradation. For residents seeking both immediate savings and long-term benefits, the synergy of DIY care with scheduled expert service is the optimum approach.
Selecting a Reliable HVAC Service Provider in Rhode Island for Seasonal Maintenance
Choosing a dependable HVAC service provider is a critical step for ensuring effective and safe seasonal maintenance. The right contractor can significantly enhance system efficiency, reduce unexpected breakdowns, and extend the lifespan of HVAC units. For property owners in Rhode Island, the selection process should include verifying licenses, insurance, customer reviews, and maintenance plan offerings. The primary point here is that well-qualified professionals provide the expertise necessary to tackle the technical challenges inherent in maintaining HVAC systems under extreme weather conditions.
A reliable HVAC contractor must hold valid state licenses and certifications, which indicate that they have met the required industry standards and regulations. Verification of insurance is equally critical, as it protects both the contractor and the property owner from liability in case of accidents or damage during service calls. Additionally, customer reviews and referrals offer valuable insights into a provider's reliability, response time, and overall service quality. Platforms such as Angie's List, Yelp, and the Better Business Bureau can serve as excellent resources for assessing a company’s reputation.
Frequently Asked Questions
Title or How often should I replace my HVAC air filters in Rhode Island?
It is recommended to replace air filters every one to three months. In environments with high dust or pet dander, more frequent changes might be necessary to maintain optimal airflow and efficiency.
What are the risks of a clogged condensate drain?
A clogged condensate drain can lead to water leakage, potential water damage, and reduced system efficiency. It may also create a breeding ground for bacteria, affecting indoor air quality.
Can I perform HVAC thermostat calibration myself?
While basic calibration can be performed using an external thermometer, in-depth calibration, especially involving wiring and sensor adjustments, is best handled by a professional to ensure accuracy and safety.
Why is professional HVAC maintenance important during autumn and winter?
Professional maintenance ensures that critical components like burners, heat exchangers, and blower motors are cleaned and inspected. This reduces the risk of carbon monoxide leaks and system breakdowns, ensuring consistent performance in extreme weather.
How does regular HVAC tune-up extend equipment lifespan?
Regular tune-ups catch minor issues before they escalate, maintain proper system performance, and reduce energy consumption. This proactive maintenance slows wear and tear, ensuring that the HVAC system operates efficiently for a longer period.
What should I look for when selecting an HVAC service provider?
Ensure the provider is licensed, insured, and well-reviewed. Check their experience with your specific system, inquire about maintenance plans, and verify their availability for emergency services. Trustworthy contractors often provide detailed service records and transparent pricing.
Is there a benefit to using smart thermostats with my HVAC system?
Yes, smart thermostats optimize temperature settings based on real-time data and occupancy, leading to improved energy efficiency and comfort. They also provide diagnostic alerts, which can preempt potential issues, contributing to overall system longevity.
Final Thoughts
Regular seasonal HVAC maintenance in Rhode Island is essential to manage the challenges presented by both humid summers and cold winters. By proactively addressing system components—from refrigerant levels to carbon monoxide detectors—property owners can significantly enhance efficiency, comfort, and safety. The balanced approach of combining DIY tasks with professional inspections ensures that systems operate optimally while minimizing energy costs. Making informed decisions about maintenance not only preserves the HVAC equipment but also contributes to a stable, healthy indoor environment.
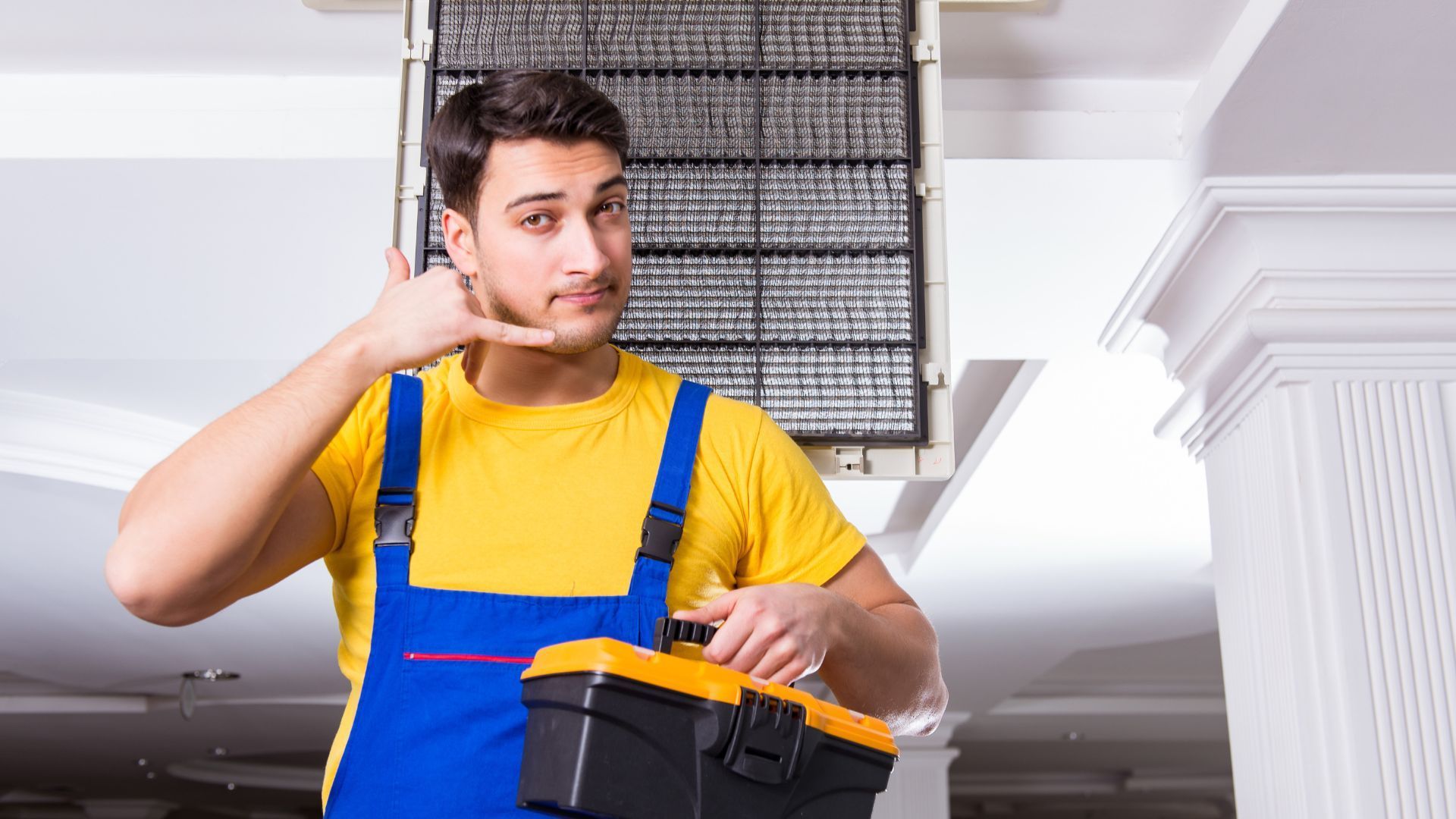
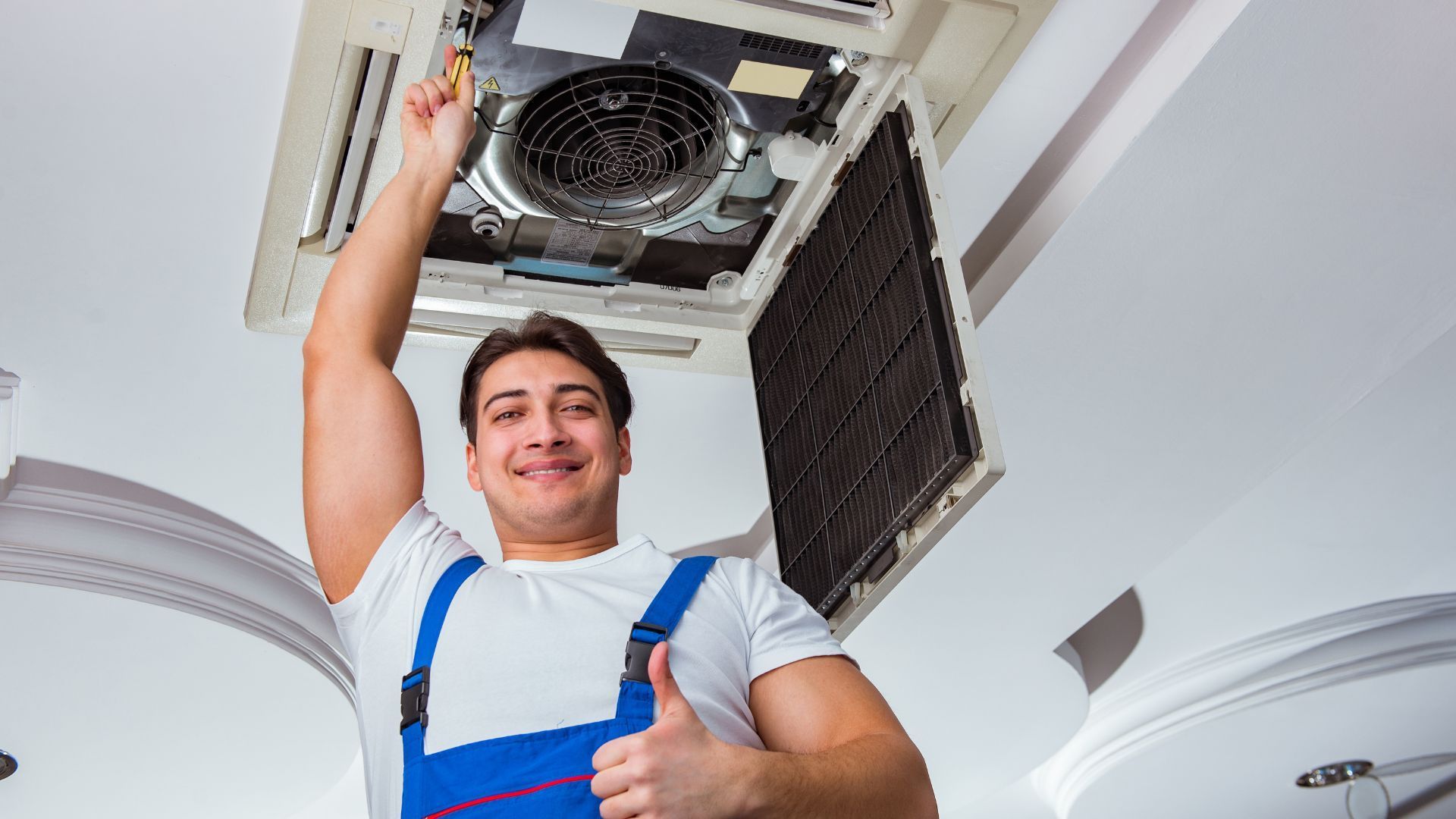
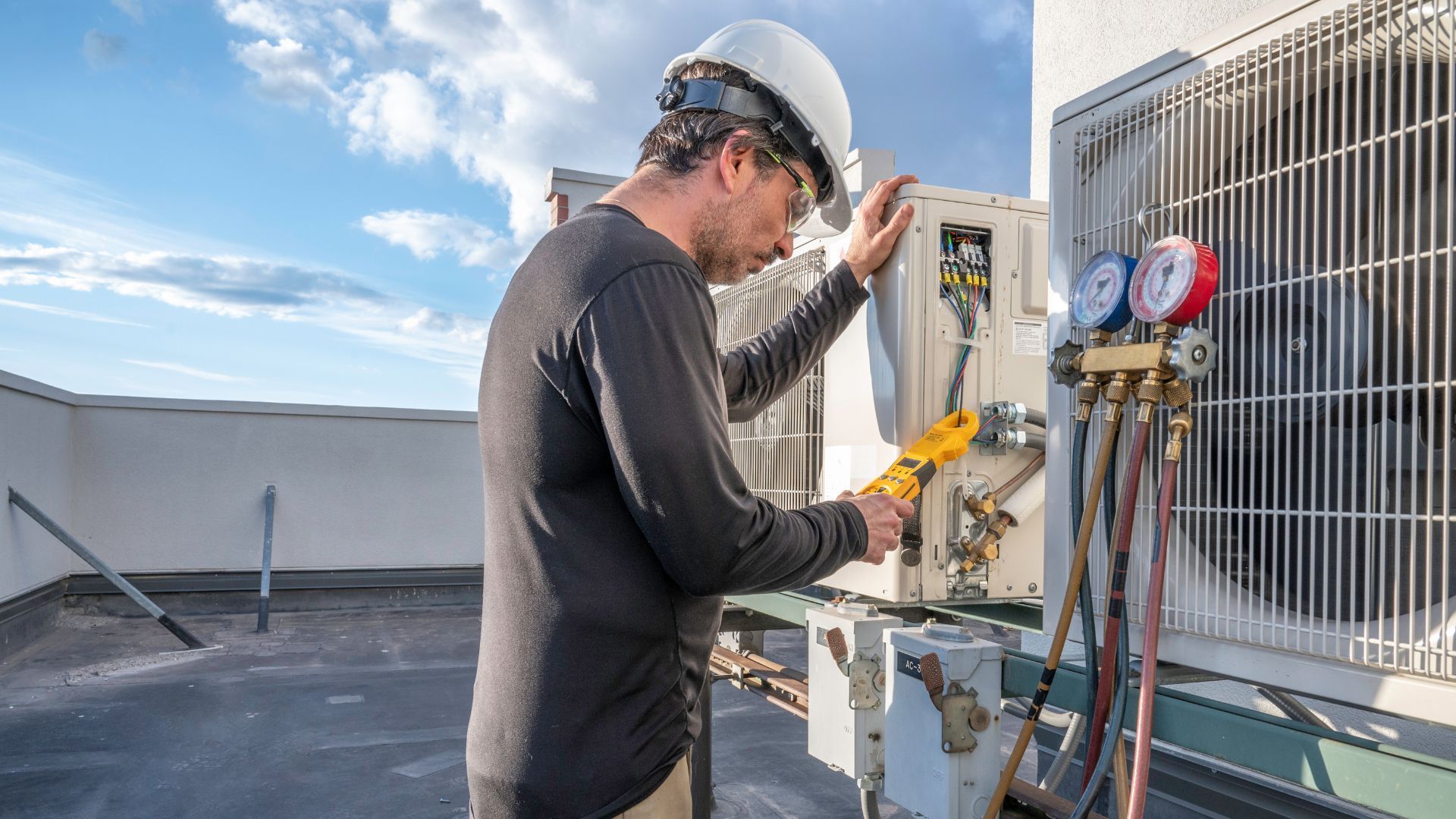
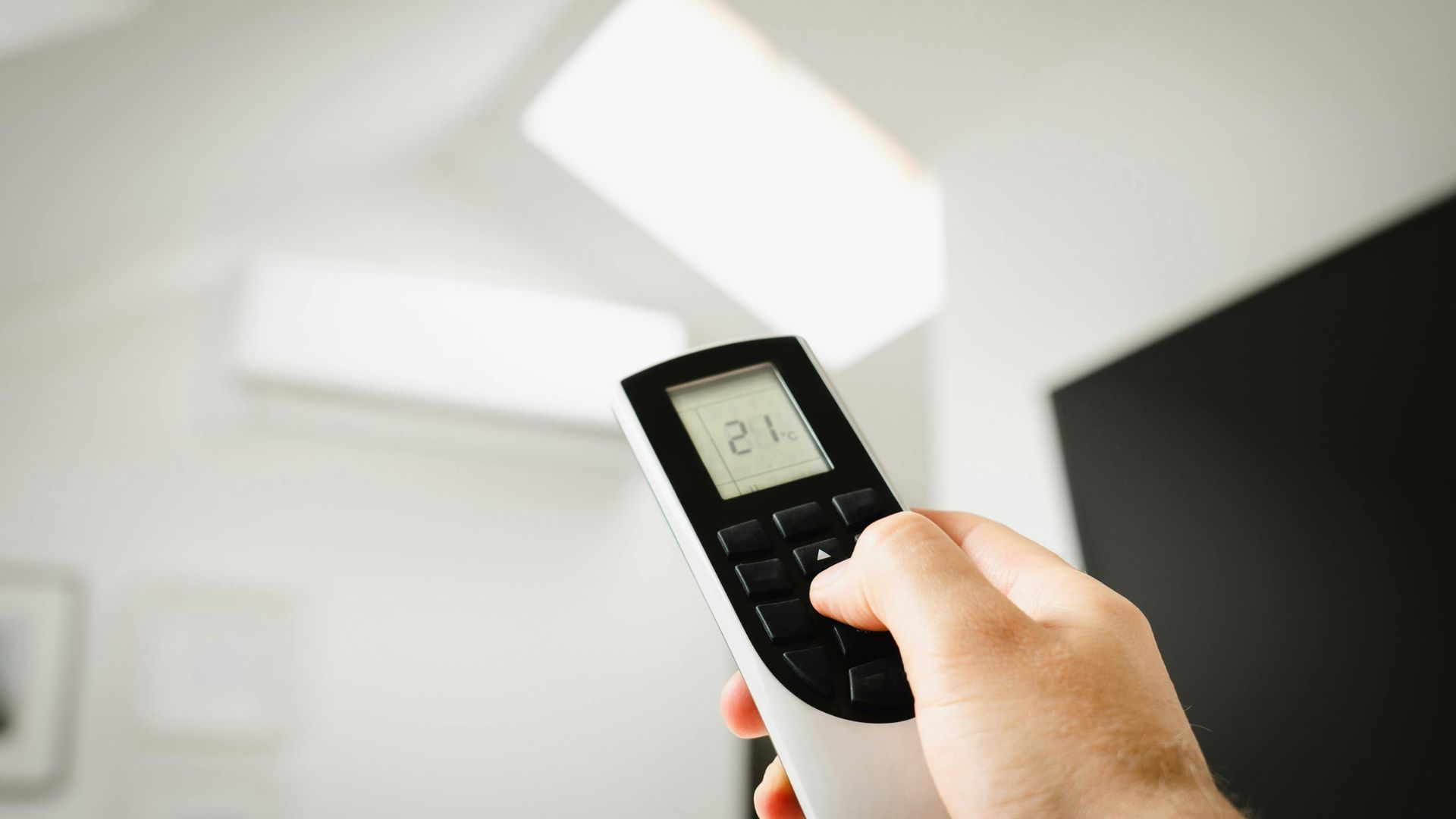
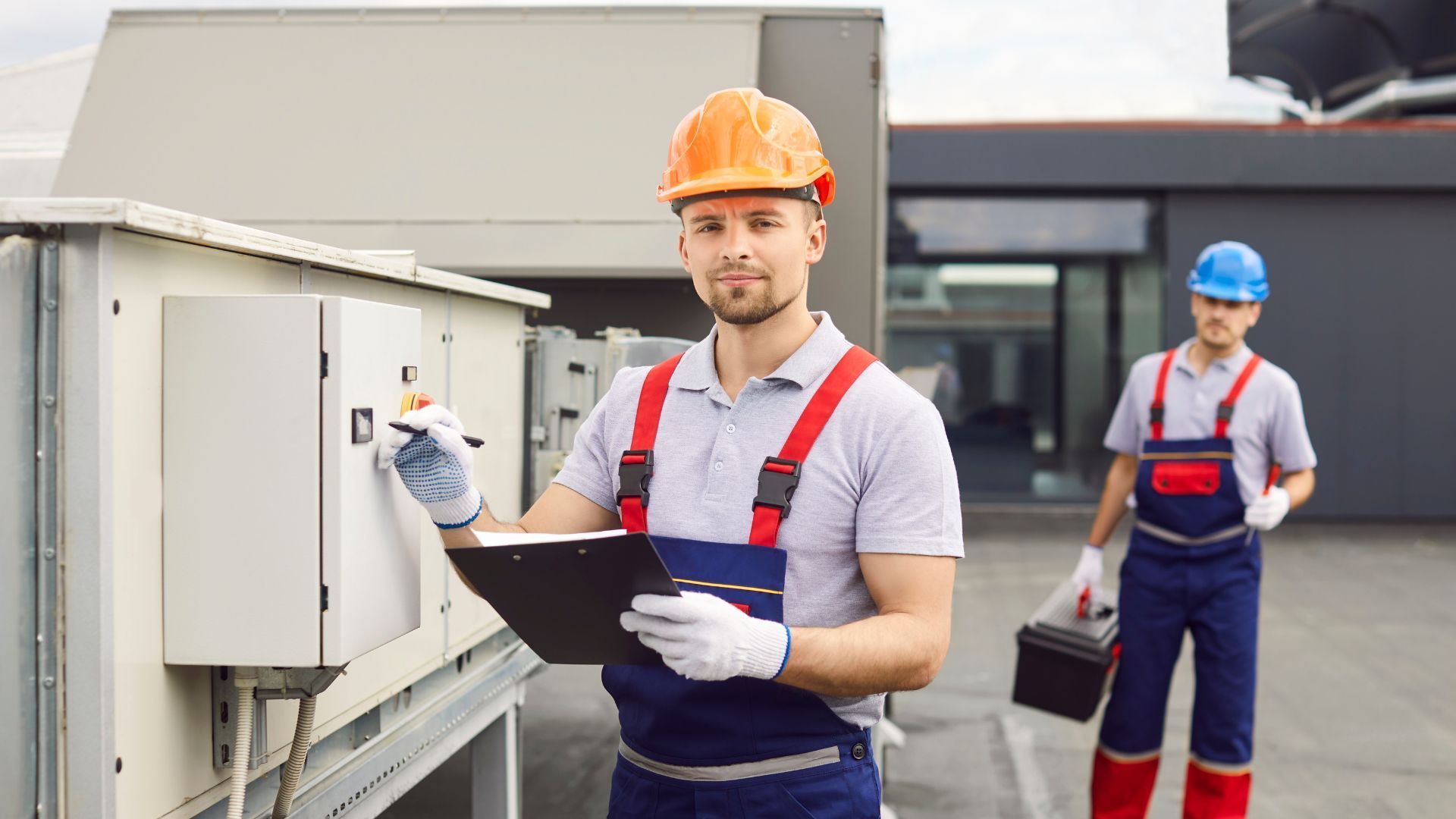
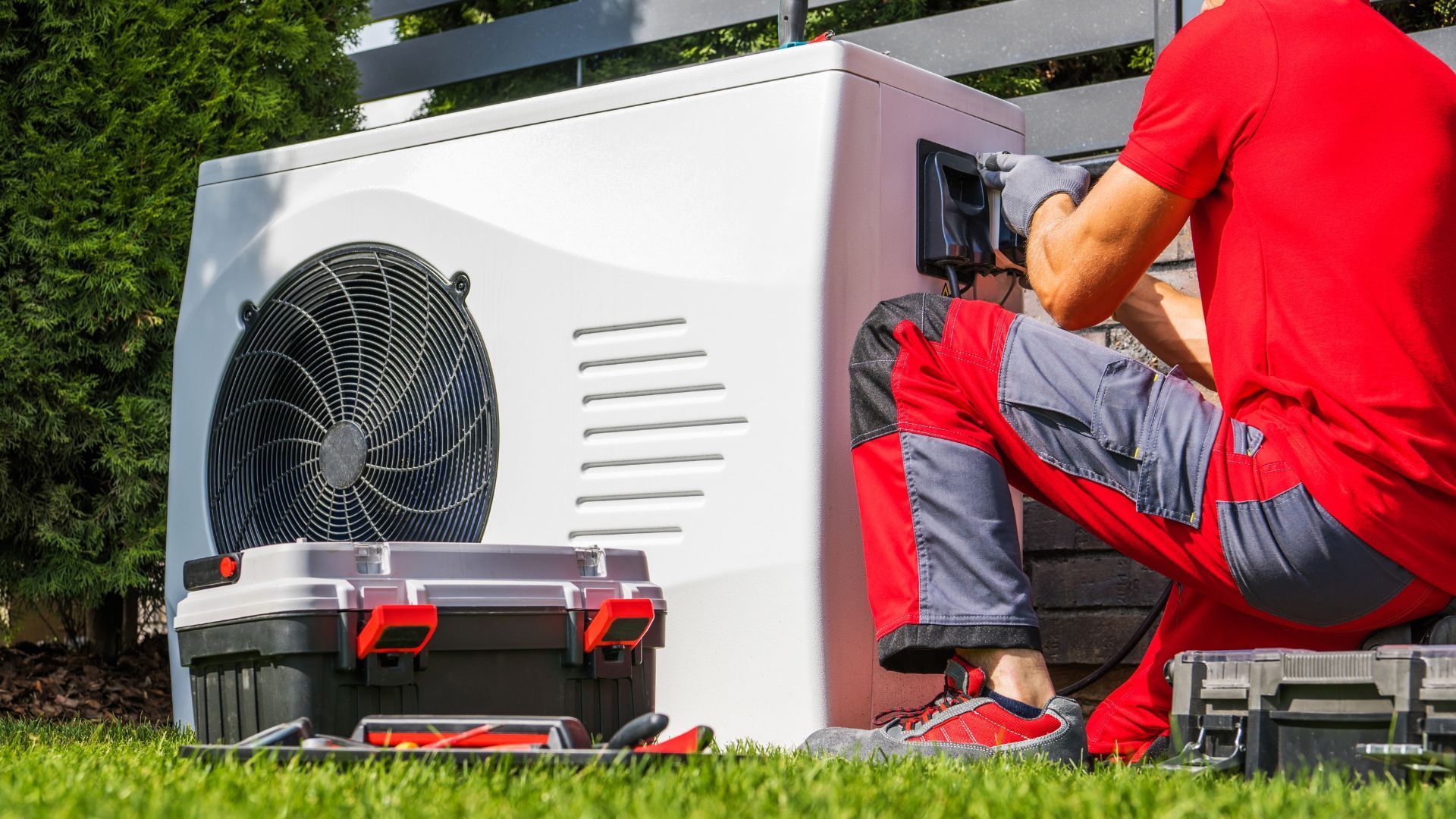
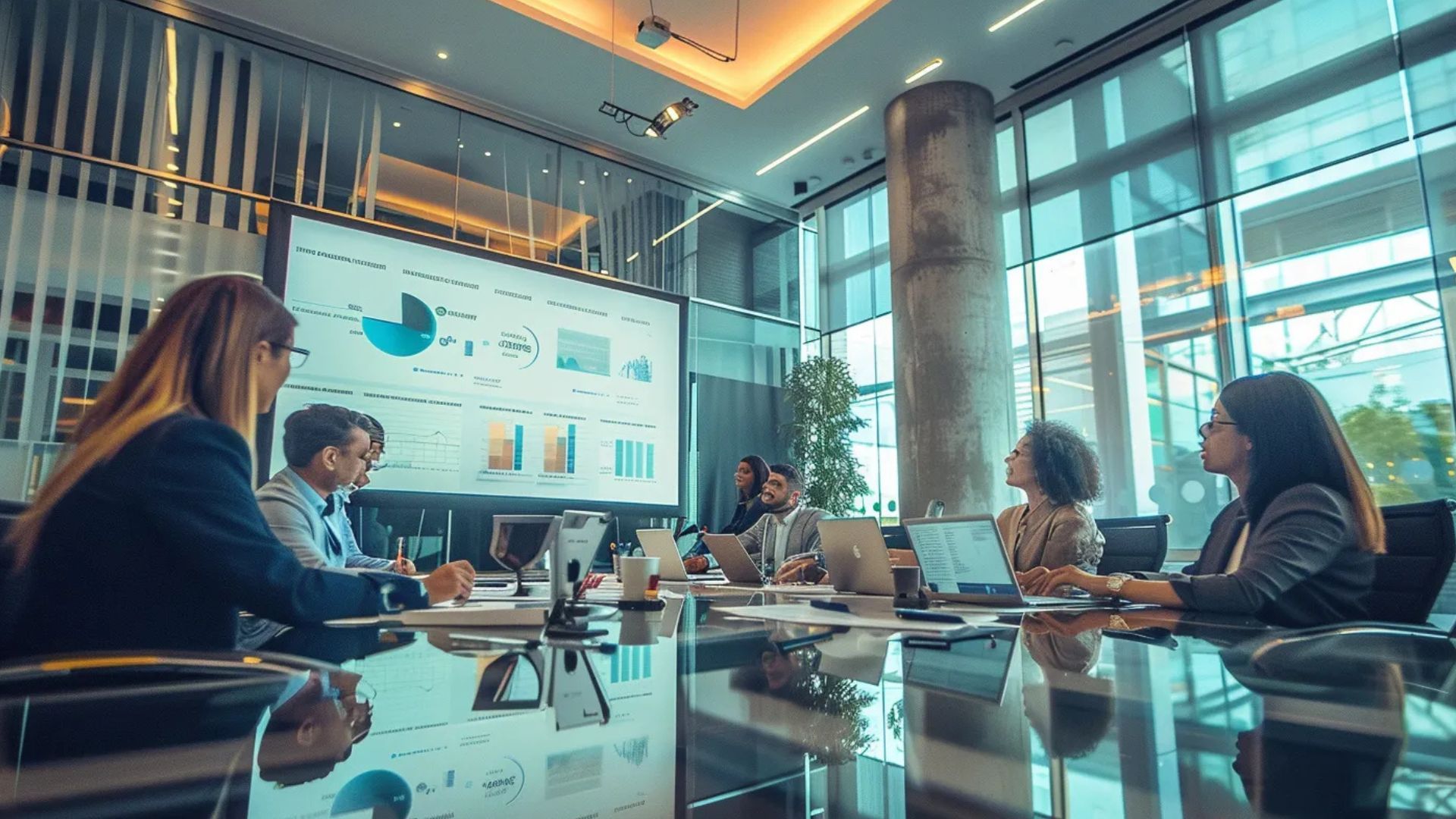